Contents
- 1. 용어 정리
- 1) 공정설계 관련 용어
- 공정설계 (Process Engineering, Process Design)
- 공정도 (process Drawing), QC공정도
- QCD (Quality, Cost, Delivery)
- 시방서, 기술사양서, 사양서 (Specification)
- MOQ (Minimum Order Quantity)
- 리드타임 (Lead Time)
- MES(Manufacturing Execution System)
- 생산계획 (Production Planning)
- 생산규모
- 생산능력 (Capacity, 케파)
- 설계능력 (Design Capacity)
- 유효능력 (Effective Capacity)
- 실제능력 (Actual Capacity)
- 이용률 (Utilization)
- 효율 (Efficiency)
- PLC (Programmable Logic Controller)
- GT(Group Technology)
- CAPP (Compuer Aided Process Planning, 컴퓨터에 의한 공정계획)
- CIPMS (Computer Integrated Production Management System, 컴퓨터에 의한 생산관리 시스템)
- CMS (Cell Manufacturing System, 셀 형 제조방식)
- VE(Value Engineering)
- MRP(Material Requirement Planning, 자재소요계획)
- ERP (Enterprise Resource Planning, 전사적 자원 관리)
- 동시공학
- 프론트 로딩(front loading)
- 스마트팩토리 (Smart Factory)
- CPS (Cyber Physics System)
- FMS (Flexible Manufacturing System, 유연생산체계)
- 생산자동화(공장자동화, FA; Factory Automation)
- 관리계획서
- OEM (Original Equipment Manufacturing, 주문자위탁생산)
- ODM (Original Development Manufacturing, 제조자 개발 생산)
- 2) 제조업 관련 용어 (기타)
- APQP (Advanced Products Quality Planning, 사전제품 품질계획)
- QC (Quality Control, 품질관리)
- QA (Quality Advance, 품질보증)
- 공차도표
- RFQ (Request for Quotation, 제안견적요청서)
- RFP (Request for Proposal, 제안요청서)
- RFI (Request for Information, 사전 정보 요청)
- RQMT (Requirement, 요구사항)
- BOM (Bil of Materials)
- 4M
- 쾌속조형 (RP; rapid prototyping)
- CAD (Computer Aided Design)
- CAM(Computer Aided Manufacturing)
- CIM (Computer Integrated Manufacturing)
- JIT (Just In Time)
- FMEA (Failure Mode and Effect Analysis)
- PFMEA (+Process)
- 풀 프루핑 (fool proofing)
- 욕조곡선 (bath-tub curve) : DFR, CFR, IFR
- 폭포수 모델, 반복적모델, 프로토타입모델
- QDM금형 (QuickDelivey Mold)
- 무접점시퀀스, 유접점 시퀀스
- 제조물책임(Product liability)
- 제조 vs 생산
- 가상공학
- DFA(조립성을 고려한 설계, Design for Assembly )
- DFM(Design for Manufacturing)
- DFMA(제조성 및 조립성을 고려한 설계)
- DFSS(식스시그마를 고려한 설계)
- All tool (양산금형 생산부품)
- Full Tool (양산공정 생산부품)
- ISIR(Initial Sample Inspection Report, 초도품 검사 보고서)
- SOP(Start of Production, 양산시점)
- IRE(Initial Risk Evaluation, 부품 초기위험도평가)
- PPAP(Production Part Approval Process, 생산부품승인절차)
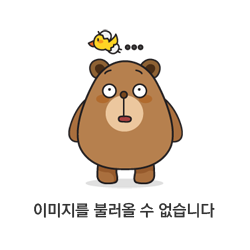
1. 용어 정리
1) 공정설계 관련 용어
공정설계 (Process Engineering, Process Design)
제조공정설계는 제품을 생산하고자 할 때 그 제품의 제조과정, 즉 공정(Process)에 관한 것으로, 원자재를 이용하여 도면을 따라 제품을 제조해 나가는 과정을 효율적으로 설계하는 것
어떤 제조과정으로 생산하느냐에 따라 제품 생산시간, 생산난이도, 생산가능여부가 달라짐
각 제조공정에서 사용해야할 장비의 선택, 도면설계상의 재조효율성, 공구의 선택, 전용기 적용 여부 등 여러가지 생산조건 또는 생산 방법에 따라 공정의 생산 효율은 달라질 수 있음
최종 결과물로는, 제작/외주 결정을 할 수 있고 공정 형태를 결정할 수 있으며 가공 방법을 결정할 수 있음
공정에는 개별공정, 흐름공정(assembly line process), 프로젝트 공정, 연속공정, 배치공정, 복합공정 등이 있음
공정설계 (Process Design)
23-4-6 공정설계에 있어서 생산 적합성 판단과 관련하여 다음을 설명하시오. (a. 생산능력의 정의와 중요성 b. 생산관련 의사결정에서 고려사항 c. 생산능력 측정의 목적과 효과 d. 생산능력 측정지
romanticdeer.tistory.com
공정도 (process Drawing), QC공정도
공정을 관리할때 "누가, 무엇을, 언제, 어떻게 관리하면 되는가"를 구체적으로 정하고 이의 요점을 공정의 흐름에 따라서 정리하고 도표에 나타낸 것으로, 품질 관리를 주안으로 한 공정관리를 위한 표준을 의미
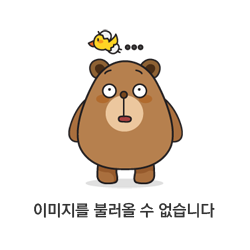
QC 공정도 (QC Flow Process Chart), 공정도 (Flow Process Chart, Process Drawing)
21-2-5 공정설계(Process Engineering)의 기능을 설명하고 공정도(Process Drawing)에 포함되어야 할 사항들에 대하여 설명하시오. 13-1-11 QC공정도를 설명하시오 1. 개요 1) QC 공정도 / 공정도 (Process Drawing)의
romanticdeer.tistory.com
QCD (Quality, Cost, Delivery)
생산공정에서 가장 중요한 품질 - 비용 - 납기. 제조업체의 성과와 밀접한 연관이 있음
품질은 제품이나 서비스가 충족해야하는 우수성 표준 혹은 사양이나 요구 사항에 대한 적합성 정도
비용관리는 제품 생산 또는 서비스 제공과 관련된 비용을 제어하고 최소화하는 활동
납기는 제품이나 서비스를 고객에게 적시에 안정적으로 제고하는 것
시방서, 기술사양서, 사양서 (Specification)
설계, 제조, 시공 등 도면으로 나타낼 수 없는 사항을 문서로 적어서 규정한 것
시방서를 사양서라고도 함. 일반적으로 사용재료의 재질·품질·치수 등, 제조·시공상의 방법과 정도, 제품·공사 등의 성능, 특정한 재료·제조·공법 등의 지정, 완성 후의 기술적 및 외관상의 요구, 일반총칙사항이 표시된다. 도면과 함께 설계의 중요한 부분을 이룬다.
설계 및 구성(치수 정보, 재질 정보 등), 기능, 성능, 품질(신뢰성), 설치(유지보수 및 지원)에 관련된 내용이 명기된다
시방서, 기술사양서, 요구사양도 (specification)
23-4-5 기술 사양서 작성에 필요한 항목 5가지를 설명하시오17-1-8 부품을 생산하는데 필요한 시방서에 표기해야 할 사항 5가지를 설명하시오 1. 개요 1) 기술사양서, 시방서, 사양서(specification)의
romanticdeer.tistory.com
MOQ (Minimum Order Quantity)
공급업체에서 1회 주문시 최소 구매 수량
공급업체, 공장 등에서 소량 주문을 무제한으로 대응해줄 수 없기 때문에 각 제조업체에서 정해놓은 최소 구매 수량
MOQ가 작을수록 제조비용이 증가한다
리드타임 (Lead Time)
상품을 거래처 또는 발주처에 주문 또는 생산하기 시작했을 때부터 입고되어 판ㄴ매가 가능할 때까지의 총 기간
MES(Manufacturing Execution System)
생상공정 내의 모든 자원 (인력, 장비, 자재)의 공정단위의 생산계획을 현장에서 실행하는 것은 물론 생산 관련 품질 데이터까지 다루는 공장정보화시스템
효율적으로 데이터를 관리하고 연동할 수 있으며, 표준화를 거친 데이터를 통합하고 관리하는 역할
제조 프로세스를 감시하고 관리하여 생산계획수립, 생산실행, 제품추적, 품질 관리 등의 다양한 작업을 통합 관리함
MES를 통해 영업관리, 생산관리, 자재관리, 설비관리, 외주관리, 공정관리, 품질관리, LOT 관리 등을 실시
생산시스템이란, 사람, 원자재, 생산 설비를 구성요소로 하여 원자재를 시장에서 가치를 갖는 제품/서비스로 변형하는 시스템.
이를 위해, ERP, MES를 이용해서, 생산관리의 기본이 되는 MRP, SCM, POP, DAS, DB와의 적절한 연계가 필요하다
MES는 제조현자의 여러 활동들을 통합적으로 관리하고 제어하는 역할, 자재의 입고부터 최종 제품의 출하에 이르기까지의 모든 공정을 실시간으로 모니터링하고 최적화하는 시스템 (스마트팩토리와 일맥상통)
핵심 기능은
실시간 데이터 관리 및 모니터링, 품질 관리, 문서화 및 규정 준수 기능
기계의 작동 상태부터 재료의 흐름, 제품의 생산 진행 상황등이 모두 포함되고 실시간으로 파악함으로써 문제가 발생했을때 즉시 대응이 가능하며 생산성 확보, 비용 절감이 가능.
스마트팩토리 (Smart Factory), 공장자동화 (FA; Factory Automation)와의 차이, CPS, ERP, MES
22-1-5 데이터 수집 측면에서 생산자동화(공장 자동화)와 스마트 팩토리(Smart Factory)의 차이점을 설명하시오. 22-1-8 스마트 팩토리의 생산시설 통합 소프트웨어 플랫폼인 CPS(Cyber Physics System)에 대하
romanticdeer.tistory.com
생산계획 (Production Planning)
공정설계란, 자원을 소비하여 가치를 창출하는 변환 과정(공정)의 비용 최소화, 수익 극대화를 실현하는 시스템으로 구축하되 이를 가장 경제적으로 구축하는 과정임
생산계획은 기업의 생산활동에 있어서 그 목적을 달성하기 위해 조직적인 예정을 수립하는 사고 활동
생산 개시에 앞서서 제품의 종류, 수량, 가격, 생산 방식, 장소, 기간 등에 대한 계획을 세우는 활동을 의미함
생산을 시작하기 앞서 판매 예측 / 주문 / 판매계획을 토대로
생산할 제품의 종류(무엇을), 생산일정(언제), 생산수량(얼마나) 등에 관하여 가장 경제적이고 합리적인 예정 (계획)
을 세우는 것.
생산 계획의 최종 목적은 생산자원의 효율적인 배분과 경제적인 생산 (생산의 최적화)이다
공정설계 7단계 중 첫번째가 기술제원 분석인데, 해당 결과를 바탕으로 생산 계획에 대한 분석이 필요 (연간 생산량, 납기 등)
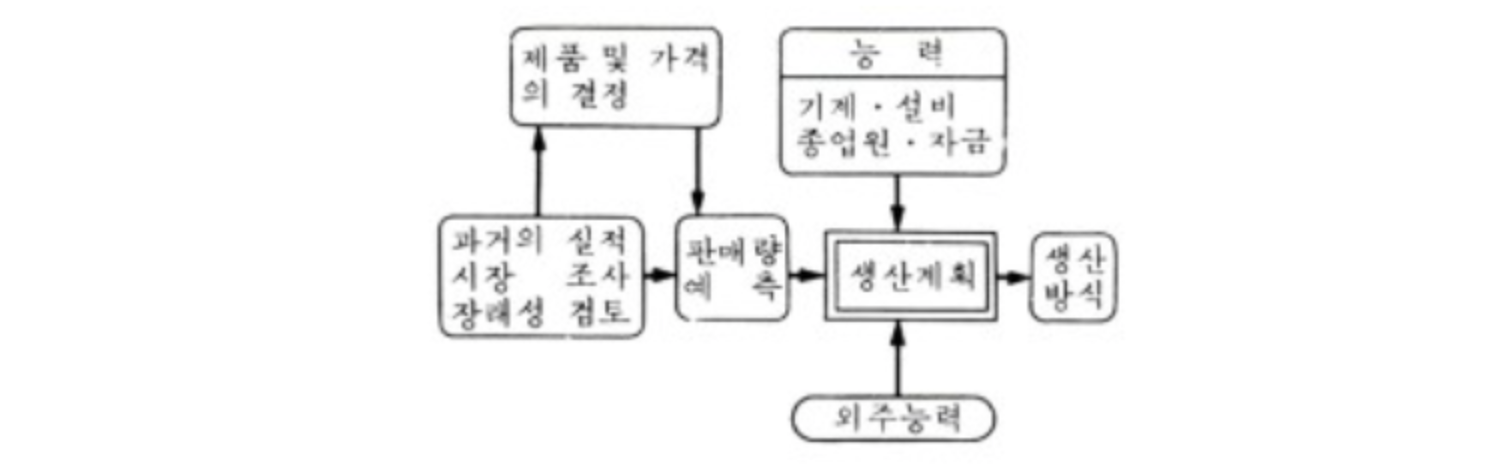
생산라인, 공장 레이아웃 (Lay out) 설계, 공자 기계 배치 방법, 공정별 배치, 제품별 배치, 셀룰러
22-3-2 생산라인에서 발생되는 각종 로스(Loss)를 최소화할 수 있는 생산라인의 레이아웃 (Lay out) 설계 시 ① 품질 ② 생산성 ③ 물류 ④ 작업자 동선 ⑤ 공간활용 ⑥ 안전 등과
romanticdeer.tistory.com
생산계획 (Production Planning), 생산 능력, 생산 적합성 판단, 가동률, 생산 능력 측정, 생산 관리
23-4-6 공정설계에 있어서 생산 적합성 판단과 관련하여 다음을 설명하시오. (a. 생산능력의 정의와 중요성 b. 생산관련 의사결정에서 고려사항 c. 생산능력 측정의 목적과 효과 d. 생산능력 측정지
romanticdeer.tistory.com
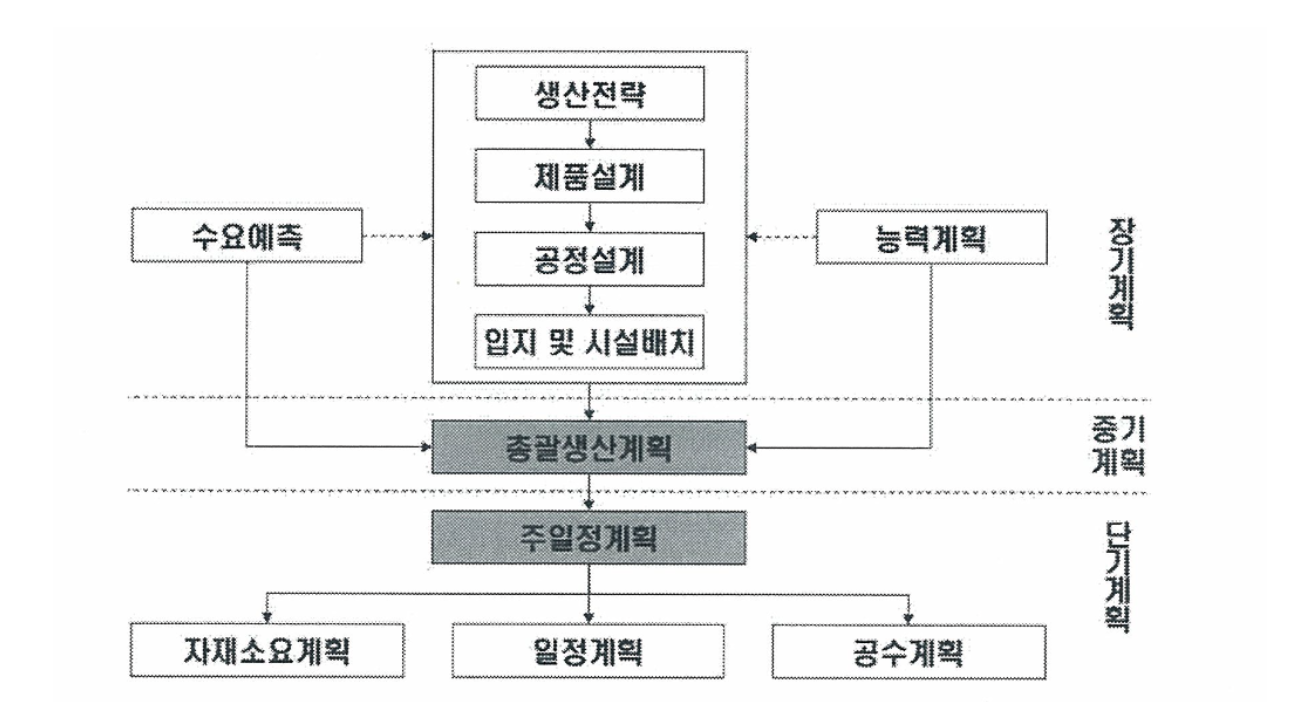
생산규모
생산계획 : 생산설비에 의해 결정 ,설비의 능력적 관점의 설비의 생산능력으로 정의 (설비나 시설의 능력)
생산능력 (Capacity, 케파)
생산계획 : 생산시스템(공정)이 정상적인 상태에서 일정 기간에 달성할 수 있는 부가가치활동의 최대 수준 (최대생산량, 영끌)
생산능력을 측정하는 이유는 제작에 필요한 비용을 최소화하는것에 궁극적인 목표가 있음
단위생산비용은 생산량의 증가화 함께 감소하다가, 일정 수준 이상이 되면 증가하기 때문에 최적 운영 수준을 찾아야함
설계능력 (Design Capacity)
설계상에 표시된 성능 내지 용량으로서 생산 시스템의 내/외부 여건에 관계없이 생산설비나 시설에서 일정기간 중 생산가능한 최대 산출량 (specification), 생산규모와 동일 의미
유효능력 (Effective Capacity)
주어진 여건에서 일정기간 중 생산가능한 사출량, 시스템 능력
실제능력 (Actual Capacity)
현재의 생산자원의 여건으로 실제 달성한 산출량
제품의 품질, 생산성 등을 극대화하는 최적 수준의 생산량
이용률 (Utilization)
실제 생산량 / 설계 능력
효율 (Efficiency)
실제 생산량 / 유효능력
PLC (Programmable Logic Controller)
산업 플랜트의 자동 제어 및 감시에 사용하는 제어장치
입력을 프로그램에 의해 순차적으로 논리 처리하고, 출력 결과를 이용해 연결된 외부 장치를 제어함
순차제어 (Sequential Control)에 사용되는 대표적인 장치
산업현장에서 기계 제어 등에 많이 사용 (특히 순차제어에 많이 사용)
여러개의 입출력을 가짐
광범위한 온도 범위에서 동작해야하고 전기적 노이즈 및 진동과 충격에 강해야함
입력에 대해 실시간 처리 능력을 가짐으로써 정해진 시간의 입력 조건에 대해 출력은 정해진 시간 안에 반응
신호처리가 빠르고 정확한 연산을 수행할 수 있음
다양한 작업을 자동으로 제어할 수 있음 조작과 유지보수가 편리함
크게 CPU, 메모리부, 전원부로 나눌 수 있음
자동화 설비, PLC(Programmable Logic Controller), 유압, 공압
19-1-13 자동화 설비에 사용되는 유압과 공기압에 대하여 각각 장단점을 설명하시오 19-2-4 PLC(programmable logic controller)의 특징과 구성요소에 대하여 설명하시오. 17-4-5 자동화 설비에 사용되는 유압
romanticdeer.tistory.com
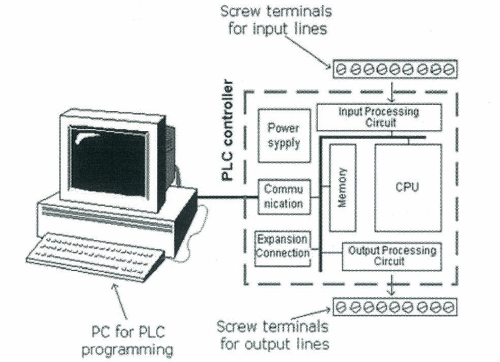
GT(Group Technology)
다품종 소량 생산을 효율적으로 실시하기 위한 하나의 원리
부품의 형상, 치수 ,가공법 등에 의거하여 유사 부품을 그룹 분류한 후 이를 바탕으로 설계를 합리화하고 준비 시간이나 가동 대기의 허비 시간을 감소시켜 다품종을 대량 생산 방식에 가까운 효과를 얻는 것을 목적으로 함
작업 준비시간, 공정간 운반시간, 가공대기시간 감소생산 수량을 증대시켜 생산성 향상 표준품의 대량생산에서 기대되는 규모의 경제를 소량생산 체계에서 실현 설계의 표준화가 가능하고 설계 비용 절감생산 일정계획이 용이해지고 MRP(자재소요관리) 적용이 수월해짐자재의 흐름이 빨라지고 (부품 이동 최소화) 생산성이 증가, 작업자 숙련도 향상 품질이 향상되고 원가가 절감, 관리가 수월해짐
코드가 같으면 설계가 불필요하여 시간이 단축되고, 공구 표준화가 가능하며, 자재 관리에서 공정간 이동시간과 대시시간을 단축시킬 수 있으며, 코드화가 되어 재고관리와 생산에서도 이점을 가져갈 수 있으며, 컴퓨터 공정계획 (CAPP)가 손쉬워짐
FMS (Flexible Manufacturing System, 유연생산시스템), GT (Group Technology, 그룹테크놀로지), 셀형 제조 방식 (
1. 개요 1) FMS (Flexible Manufacturing System) 정의 여러 가지 부품 유형들의 혼합과 수요 패턴 변화에 따라 조정되는 생산량에 유연하게 대응하기 위해 1) 여러 작업장에서 다양한 부품 유형을 동시에 처
romanticdeer.tistory.com
(1) 소재의 재질, 형상, 제작방법, 가공설비 등이 유사한 것끼리 분류하는 방법
- 육안검사
- 제조공정해석
- 부품분류 코딩 시스템 (부품의 설계 방법과 제조 방법에 코드를 명기하여 필터링하는 방법)
가공물의 형상, 치수, 가공방법, 작업준비, 가공설비, 조립, 공정, 측정 방법을 기초로 분류하는 시스템
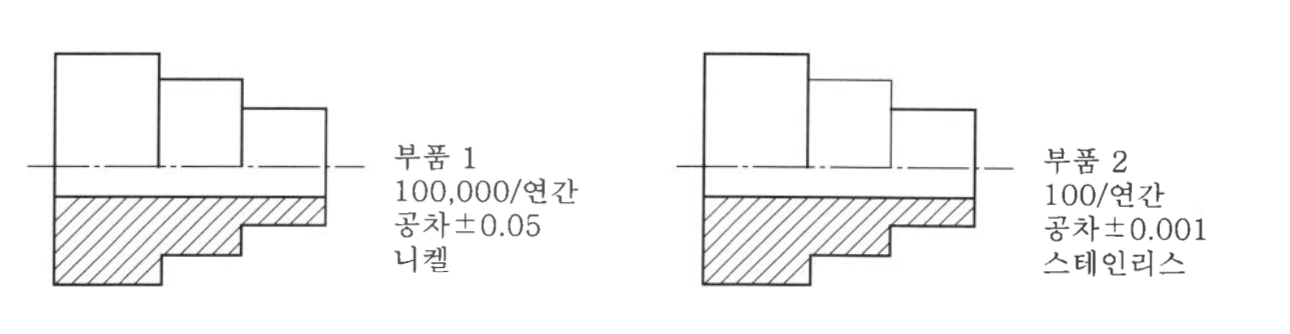

CAPP (Compuer Aided Process Planning, 컴퓨터에 의한 공정계획)
전문가가 현장 노하우 및 작업자 의견, 공작기계의 특성을 컴퓨터에 일정한 형식으로 입력해놓아, 사용자가 컴퓨터 프로그램을 통해 쉽게 공정도 등을 작성할 수 있게 구축해 제품 생산의 극대화를 꾀하는 시스템. 재생식 CAPP, 창생식CAPP로 구분된다
공정의 합리화, 공정계획자의 생산성 향상, 소요시간 단축, 이해도 증진, 다른 시스템과의 연계성을 확보할 수 있음
CIPMS (Computer Integrated Production Management System, 컴퓨터에 의한 생산관리 시스템)
컴퓨터를 통한 생산관리시스템
최근 MES (Manufacturing Execution System)과 역할이 동일하며, 구성 요소로는 기술, 생산 데이터 베이스, 자재수급계획(MRP), 용량계획, 재고관리, 공장관리 등으로 구성됨
재고 관리로는 원자재와 구매부품 재고, 가공품 재고, 완제품 재고, 보수/수리/공구 재고의 적정 수준을 유지하여 불필요 투자를 최소화하며, 자재수급계획(MRP; Material Requirement Planning)에 기초한다.
CMS (Cell Manufacturing System, 셀 형 제조방식)
자동화된 핵심 가공기능, 자동화되어있는 내부 반복기능의 제어 기능을 가지고 있음
CMS는 그것 자체로써 단독 가동이 가능한 소규모의 FMS개념, 외부 반송 시스템과 연결하면 FMS의 기본 모듈이 될 수 있음 (모여서 더 큰 FMS를 구성)
CMS는 FMS에 비해 규모가 작고 중소기업에 도입이 용이함
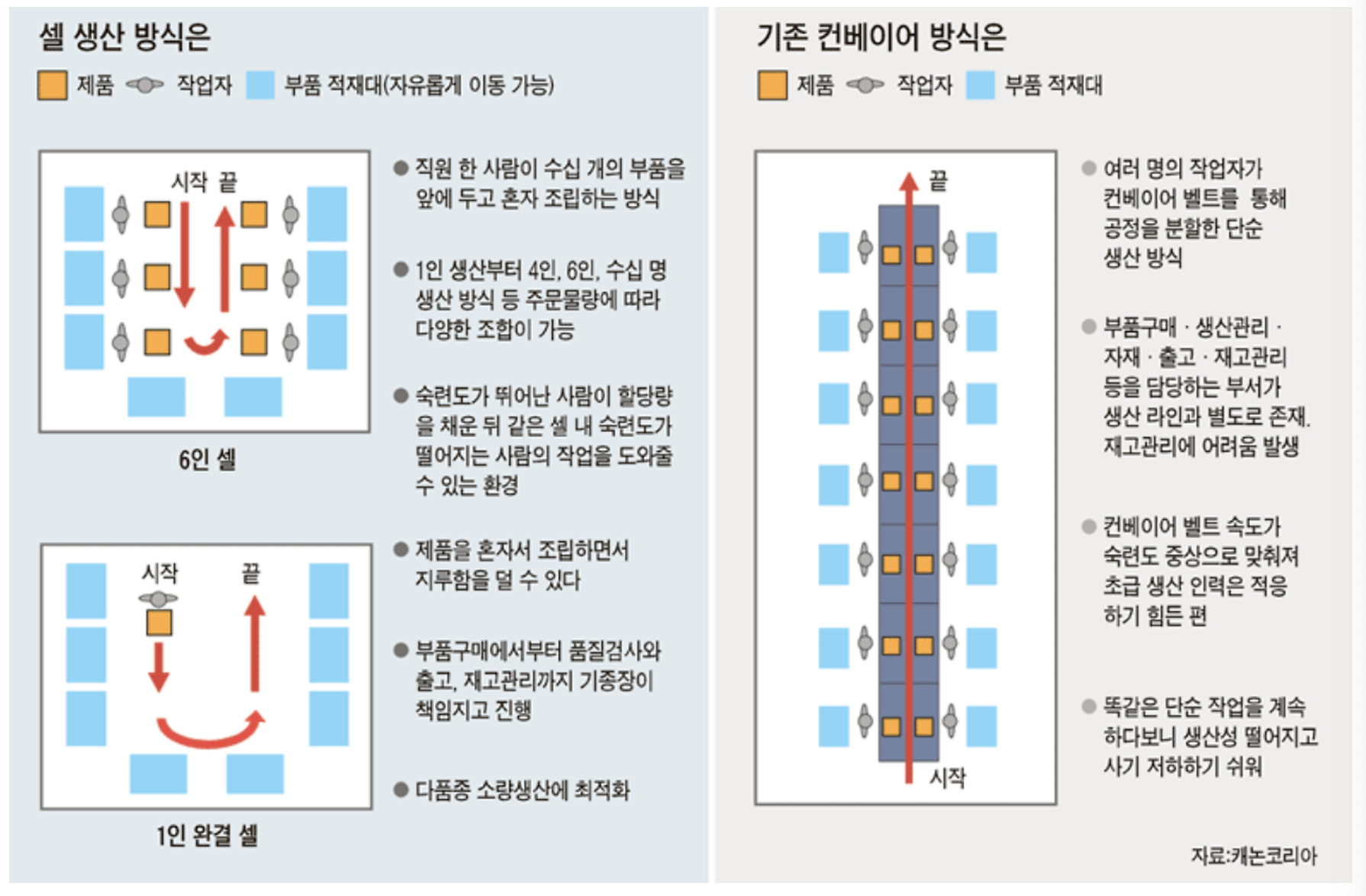
VE(Value Engineering)
VE는 단순 원가절감이랑은 다른 개념이다.
VE는 설계의 경제성에 관하여, 최소의 생애주기 비용으로 시설물의 필요한 기능을 확보하는 방법이다.
즉, 그 기능 또는 성능을 유지 혹은 향상시키기 위한 가장 경제적인 방법을 찾아가는 과정
가장 싼 가격으로 가장 좋은 효과를 내는 과정
V = F / C
V : 가치 (Value), F : 기능 (Function), C : 총 비용, 생애주기비용 (Cost)
가치공학(VE; Value Engineering)
21-4-8 VE(Value Engineering)의 기능적 형태 4가지를 설명하고 VE 단계별 추진내용에 대하여 설명하시오.19-2-1 가치공학(value engineering)의 정의, 목적을 쓰고, 원가 산정방법 중 가치향상 패턴에 대하여
romanticdeer.tistory.com
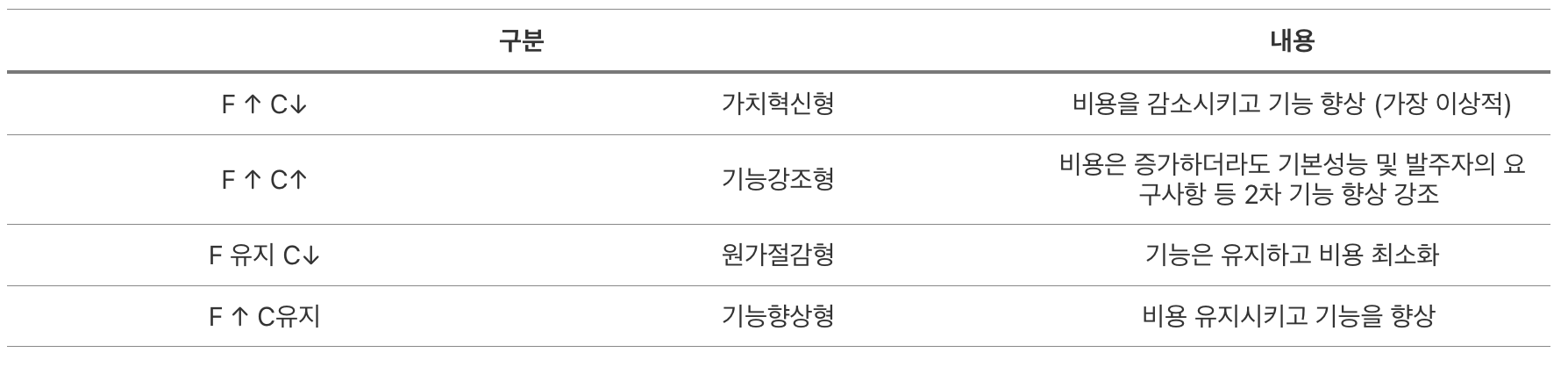
MRP(Material Requirement Planning, 자재소요계획)
MRP는 제품을 구성하는 모든 요소 - 원자재, 반 조립품, 완제품 등에 대한 자재 수급 계획과 생산관리를 통합시킨 제조 정보 관리 기술/시스템임
MRP는 BOM(Bill of Material), 표준 공정도 (Process chart), 표준 생산 계획(Master Production Scedule), 재고 레코드 (Inventory Record) 등의 정보로 구성되며 이를 근거로 어떤 물건이 언제, 어느곳에서 얼마나 필요한지 예측하고 모든 제조활동과 관리 활동이 같은 계획에 근거하여 움직이기 때문에 자원의 비능률적인 활용이나 낭비를 제거할 수 있음
"MRP는 종속 수요 품목의 생산, 구매, 재고관리를 합리적으로 처리하는 통합적인 생산계획 및 재고관리의 전산화된 관리시스템"
MRP(Material Requirement Planning, 자재소요량계획)
12-1-7 자재소요계획(MRP)의 장점과 단점을 설명하시오 1. 개요 1) MRP (Material Requirement Planning) 정의 제품의 생산수량 및 일정을 토대로 그 제품 생산에 필요한 원자재, 부분품, 공산품, 조립품 등의
romanticdeer.tistory.com
ERP (Enterprise Resource Planning, 전사적 자원 관리)
재무, 인사, 제조, 구매, 서비스 등 여러 프로세스 전반을 통합하여 효율적인 관리를 할 수 있는 시스템
업무의 통합화 (ex. 재무, 판매는 업무는 나뉘어 있지만 프로세스는 유기적으로 연결 → 유기적으로 연계가 필요)
표준 프로세스의 내장
그룹웨어와의 연동 (전사 통합 시스템)
개방형 시스템
동시공학
제품 개발 단계에서 관련된 조직이 초기에 참여하여 다수의 단계가 동시에 진행, 오류를 조기에 발생 및 해결함으로써 개발 기간을 단축시키는 방법론
설계초기단계에서부터 제품의 고유 기능 뿐 아니라 제조, 조립, 검사, 서비스 용이성, 법규, 인증, 사용성 등까지 한꺼번에 검토하여 개발 기간을 단축시키고 개발 비용을 절감하여 품질 및 생산성을 향상시킨다
동시공학에는 4C가 존재한다
- 동시성(Concurrence, 제품설계와 공정설계가 동시에 이루어짐)
- 제약성(Constraints, 공정은 제품 설계에 제약을 줌)
- 협조성(Coordination, 최선의 품질과 비용 그리고 납기를 준수하기 위해 제품과 공정이 서로 협조
- 합의성(consensus) : 동시공학 팀 내 모든 구성원들이 합의하에 의사결정
프론트 로딩(front loading)
프런트로딩혁신이란 후속절차에서 발생할 잠재적 문제를 앞 단계에서 미리 확인하고 해결하는 것. 불필요한 낭비를 줄이기 위해 미리 사전점검을 벌여 시행착오를 줄이는 것. (FMEA와 유사)
스마트팩토리 (Smart Factory)
생산 전략에 기반을 둔 제조 여건 변화에 '유연'하게 대응하고 공금망 관리 (SCM ; Supply Chain Management), 통합 관점의 QCD (Quality, Cost, Delivery) 및 제약사항 관리로 생산 운영을 신뢰성 있게 수행하며 유기적으로 연결되는 공장을 의미
미래형공장, 지능형 공장이라 불리는 스마트 팩토리는 디지털 데이터와 ICT 기술을 결합해 디지털 자동화 시스템으로 운영되는 새로운 플랫폼으로, 인력 의존도가 높았던 전통적인 제조업의 한계에 대한 대안
센서를 비롯한 IoT (Internet of Things), 로보티스기술, CPS(Cyber Physics System), MES (Manufacturing Execution System), ERP (Enterprise Resource Planning), 빅데이터 및 AI로 구성됨
스마트팩토리 (Smart Factory), 공장자동화 (FA; Factory Automation)와의 차이, CPS, ERP, MES
22-1-5 데이터 수집 측면에서 생산자동화(공장 자동화)와 스마트 팩토리(Smart Factory)의 차이점을 설명하시오. 22-1-8 스마트 팩토리의 생산시설 통합 소프트웨어 플랫폼인 CPS(Cyber Physics System)에 대하
romanticdeer.tistory.com
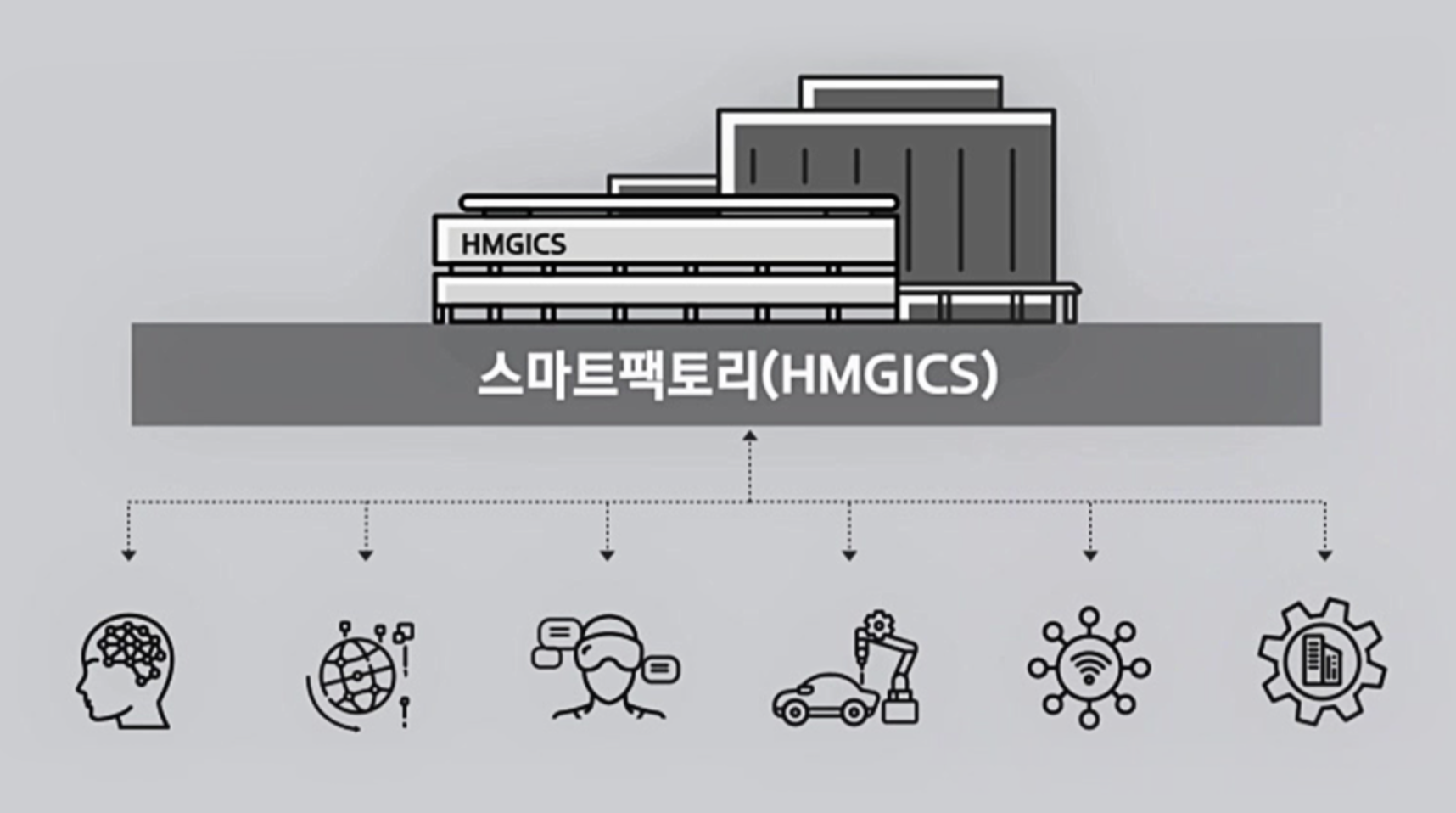
CPS (Cyber Physics System)
스마트 팩토리의 생산시설 통합 소프트웨어 플랫폼
실제 세계와, 여기서 진행되는 다양하고 복잡한 업무, 공정과 정보를 사물인터넷 등 네트워크를 통해 데이터에 접근, 처리, 관리하는 개방형 서비스를 기반으로 사이버 세계의 디지털 모델에 긴밀하게 연결, 활용하는 컴퓨터 기반 구성 요소와 시스템
CPS는 디지털 트윈과 흡사하며 의미는 일종의 공장을 위한 가상 셰계 (메타 팩토리)를 뜻함 : 가상 세계에 똑같은 공장을 건설하고 똑같은 방식으로 작동하고 구현함
Big data & AIr기술, IoT기술, Digital Twin 기술이 결합되어 구성되어있음

FMS (Flexible Manufacturing System, 유연생산체계)
여러 가지 부품 유형들의 혼합과 수요 패턴 변화에 따라 조정되는 생산량에 유연하게 대응하기 위해
1) 여러 작업장에서 다양한 부품 유형을 동시에 처리 가능한 생산의 유연성과 2) 생산성을 동시에 지향하는 생산 시스템
대표적으로 MCT, CNC 가공등을 활용.
공작기계는 아래 기능을 기본적으로 보유하고 있음
공구의 자동 공급 및 교환 기능 (ATC; Auto Tool Changer)공작기계 내 측정 기능무인 운전과 원격 운전을 위한 각종 제어 및 자동 보정 기능들과 같은 자동화를 위한 하드웨어 기업 내 상위 정보시스템과 통합 기능을 갖는 소프트웨어 (CPS, 스마트팩토리)
FMS (Flexible Manufacturing System, 유연생산시스템), GT (Group Technology, 그룹테크놀로지), 셀형 제조 방식 (
1. 개요 1) FMS (Flexible Manufacturing System) 정의 여러 가지 부품 유형들의 혼합과 수요 패턴 변화에 따라 조정되는 생산량에 유연하게 대응하기 위해 1) 여러 작업장에서 다양한 부품 유형을 동시에 처
romanticdeer.tistory.com
CNC가공, NC 가공, 서보기구(servo mechanism), 공구제어방법, CNC 주축 열변위특성
19-1-8 CNC 공작기계에서 공구의 이동경로와 형상에 따른 제어 방법 3가지에 대하여 설명 하시오. 19-3-6 CNC 공작기계의 정의, 구성, 기계가공의 흐름에 대하여 설명하시오. 19-4-4 CNC 공작기계의 서보
romanticdeer.tistory.com
생산자동화(공장자동화, FA; Factory Automation)
제품의 설계에서 제조, 출하에 이르기까지 공정을 자동화하는 기술
컴퓨터 시스템이나 산업 로봇을 도입해 공장의 무인화와 생산 관리가 자동화되는 시스템
스마트팩토리와 다른점은 1) 공정자동화는 수직적 통합(생산시스템에 한함), 2) 공정들간에 유기적인 연결 X, 3) 자동화 수준이 낮음, 4) 생산물량 예측 및 유연화 대응 불가능
관리계획서
제품의 제조를 관리하는데 요구되는 시스템 및 프로세스의 서면 기술
OEM (Original Equipment Manufacturing, 주문자위탁생산)
주문자의 설계에 따라 제품만 생산하여 주문회사에게 납품하는 형태
주문 회사의 상표를 붙여 소비자에게 판매됨
공장과 생산설비를 가지고 있는 회사가, 그렇지 않은 회사의 물건을 만들어서 납품. 기술력보다는 설비의 유무가 영향이 더 큼
(설계 능력이 없고 단순 생산 Only)
ODM (Original Development Manufacturing, 제조자 개발 생산)
OEM과 동일하게 제조자의 상표가 아닌, 주문자의 상표가 부착되는 점은 동일하나 제조자의 제품 설계 / 개발 과정 참여 여부가 다름
제조업체가 기술력을 바탕으로 제품을 개발, 생산까지 한 뒤 판매까지 하는 시스템 (주문업체의 상표를 붙여)
판매업체(주문업체)는 자사의 브랜딩과 로고만 활용하는 방식
2) 제조업 관련 용어 (기타)
APQP (Advanced Products Quality Planning, 사전제품 품질계획)
사전에 제품의 품질을 확보하기 위한 목적으로 만드는 품질 분야 계획
■ APQP Phase 1 Project Planning
1. Design Goals 설계목표
2. Reliability & Quality Goals 신뢰성 및 품질목표수립
3. Preliminary Bill of Materials 예비 BOM
4. Preliminary Process Flow 예비 공정흐름도
5. Preliminary Listing of Special Product & Process Characteristics 예비 특별특성 목록표
6. Product Assurance Plan 제품 보증계획
■ APQP Phase 2 Product Design and Development
1. Design FMEA 설계고장모드영향분석
2. DFMA, Design for Manufacturing and Assembly 제조와조립용 설계
3. Design Verification 설계검증
4. Design Reviews 설계검토
5. Prototype Build 시제품제작
6. Engineering Drawings 설계도면
7. Engineering Specifications 설계시방서 (설비 엔지니어링, 설계, 제조에 대한 구체적인 세부사항 규정)
8. Material Specifications 자재시방서
: 작업에 필요한 재료, 장비, 시스템, 표준 및 제작 및 관련 서비스의 수행에 대한 서면 요구 사항
9. Drawing & Specification Changes : 설계 및 시방서 변경이력
10. New Equipment(Tooling & Facilities Requirements) : 설비, 툴, 장비 요구사항
11. Special Product & Process Character istics 특별특성
12. Prototype Control Plan : 프로토타입 관리계획서
13. Gages/Testing Equip. Requirements : 계측기, 검사장비 요구사항
■ APQP Phase 3 Process Design and Development
1. Packaging Standards 포장표준
2. Product/Process Quality System Review 품질시스템검토
3. Process Flow Chart 공정흐름도
4. Floor Plan Layout 현장 레이아웃
5. Characteristics Matrix 특성매트릭스
6. Process FMEA 공정실패모드영향분석
7. Pre-Launch Control Plan 양산전 관리계획서
8. Process Instructions 공정지침서
9. Measurement Systems Analysis Plan 측정시스템분석 계획
10. Preliminary Process Capability Study Plan 예비공정능력연구 계획
11. Packaging Specifications 포장사양서
■ APQP Phase 4 Product & Process Validation
1. Production Trial Run 양산성테스트 production demostration run 또는 run at rate라고도 부름
2. Measurement Systems analysis : 측정시스템분석
3. Preliminary Process Capability Study : 예비공정능력평가
4. Production Part Approval : 부품승인
5. Production Validation Testing 제품검증테스트
6. Packaging Evaluation 포장평가
7. Production Control Plan 관리계획서
8. Quality Planning Sign Off 품질 계획 승인
QC (Quality Control, 품질관리)
기업 자체의 필요성에 의해 자율적으로 추진되는 품질관리를 위한 실시기법과 활동
QC에서 말하는 품질은 생산 중 심적 내지는 제품 중심적 사고와 관리기법을 말함.
품질에 대한 요구사항을 만족시키기 위해 사용하는 활동들 (품질에 대한 요구사항을 만족시키기 위해, 최종 제품에 대한 품질 이상유무 판단 및 개선 활동)
제품 검사 및 테스트, 불량품 감지 및 대처, 품질 데이터 분석 및 보고를 통해 고객만족, 비용절감, 경쟁력 강화
QA (Quality Advance, 품질보증)
제품이나 서비스가 처음부터 끝까지 양질로 유지되도록 전반적인 과정을 관리하는 행위
문제가 생기지 않도록 예방하는데 그 중점을 두는데, 계획, 시스템, 문서화, 정책 등을 통해 품질을 관리하고 프로세스가 잘 작동하도록 하는 활동
공차도표
부품의 제조과정에서 공정치수 및 공차를 합리적으로 설정, 검토, 조정하는데 사용하는 자료
공차관리도, 공차도표, 공차표 등으로 불림
공차 도표
12-4-5 공정설계시 공차도표의 목적을 설명하시오 1. 개요 1) 공차도표의 정의 부품의 제조과정에서 공정치수 및 공차를 합리적으로 설정, 검토, 조정하는데 사용하는 자료 공차관리도, 공차도표,
romanticdeer.tistory.com
RFQ (Request for Quotation, 제안견적요청서)
(갑이 을에게 요청하여 을이 갑에게 제출)
RFP와 같이 요청함. 예산과 견적 포함. 제품이나 서비스에 대한 공식적인 견적가 요청서
부품개발에 요구되는 성능과 사양을 평가하여 설계에서 업체로 제시하는 사양 및 제원이 명확해야함
일반적으로 특정 작업을 아웃소시하거나 하청, 생산시 사용
해당 서비스나 제품을 만들기 위해 얼마가 드는지 기술한 문서
RFP (Request for Proposal, 제안요청서)
(갑이 을에게 보내는 문서)
스펙이 제대로 정해져있지 않거나, 협력사의 제안을 통해 공급업체를 선정하는 경우 사용되는 요청서
1차로 선별된 업체들한테 보내는, 원하는 요구사항을 정리한 문서, 주제 목적 목표 내용 기대성과 등
프로젝트에 대한 상세한 정보가 나와있음
(프로젝트 제목, 목적 및 목표, 내용, 기대성과, 수행기간, 금액, 참가자격, 제출서류목록,기타ㅓ요구사항 등
RFP에 의거하여 공급사 (수행사)는 제안서를 작성해서 제출
보통 RFP를 뿌릴때 RFQ를 같이 요청함
RFI (Request for Information, 사전 정보 요청)
(갑이 을에게 요청하여 을이 갑에게 제출)
발주사가 제안요청서 (RFP)를 보내기 전 프로젝트 계획 및 수행에 필요한 정보를 얻기 위해 공급사들에게 정보를 요청하는 것
해당 내용으로는, 기업정보, 보유기술, 제공할 수 있는 제품 정보, 서비스 소개, 시장 동향, 주요 경쟁사 및 기존 작업 내역 예시 요청
RQMT (Requirement, 요구사항)
각종 설계 및 공정에 사용되는 요구사항의 줄임말
BOM (Bil of Materials)
부품리스트, 자재명세서
제품을 구성하는데 필요한 원자재, 부품 또는 부분 조립품의 소요량과 조립순서, 가공순서를 나타내는 자료
4M
4M이란 Man, Machine, Material, Method의 약자로, 제조업에서 매우 기본이고 중요한 요소.
결국 4m을 바탕으로 계획, 준비, 실행이 결정되어 제조업의 최종 목표인 QCD 달성을 향해 나아간다
쾌속조형 (RP; rapid prototyping)
3D프린팅 관련 기술을 활용하는 공정 또는 산업을 말하며 이러한 기술을 사용 하는 산업은 이제 우주, 항공, 자동차, 의료, 소비재 제품, 건축, 문화재 복원, 예술, 패션, 가 구, 조명, 주얼리, 디자인 분야까지 다양하다. AM 즉 Additive Manufacturing (Rapid prototyping과 동일 의미)은 단어적 해석을 하 면 첨가가공 또는 부가제조 정도이며 이 단어가 나오게 된 내력에는 바로 3D 프린팅 조형 가술 원 리 때문이다. 30 프린팅은 컴퓨터로 제작된 디지털 CAD 데이터를 손으로 만질 수 있는 물리적인 모델로 빠르고 정확하게 제작하는 조형기술이다.
CAD (Computer Aided Design)
컴퓨터 지원설계, 컴퓨터에 기억되어 있는 설계 정도를 디스플레이를 통해 추출하여 화면을 보며 설계하는 것.
CAM(Computer Aided Manufacturing)
CAM은 생산에 관한 공정설계나 작업설계라고 하는 넓은 의미로 해석할 수도 있고, 좁게는 CAD데이터에 따라 기계가공용 NC프로그램을 작성하는 가공준비작업(주로 이렇게 해석함)
CAM시스템의 특징 : 종합적인 데이터베이스의 일원화, CAE지원(해석, 시뮬레이션), 형상정의기능의 향상, CAM기능의 충실, 다양한 통신 기능 지원
세부 기능 : 모델링에서 서피스 모델 추출, 3차원 곡면생성, NC공정을 위한 자동공정설계기능, NCCODE (G코드 등) 생성, 절삭패턴제어기능(등고선, 방사선, 전삭), 공구경로 데이터 확보, 절삭조건 및 공구수명관리, 시물레이션 및 검증 기능, 실시간 모니터링 기능 등
CAD : AutoCAD, SOlidworks, FUsion, Inventor, PROE, CATIA
CAM : Hyper FORM, Power Mill, Pro CAM, CATIA, CAMAX, Master CAM, NG CAM, Work NC, UG NX, Hyper Mill, CADCAM
CIM (Computer Integrated Manufacturing)
컴퓨터 네트워크 기술을 이용하여 물건과 정보의 흐름을 이체화 시켜 경영 효율화를 이루기 위한 자기통제기능을 가진 유연한 생산시스템 (CAD, CAM, PPC(Production Planning & Control), FA(생산자동화기술), IT(정보기술))
FMS(Flexible Manufacturing System)은 생산현장의 자동화, 생산설비의 성능 향상에 대하여 다양화된 요구의 대응과 간소화를 목적으로 함
CAD/CAM/AI/MRP/JIT/시스템기술/네트워크기술/데이터베이스기술
MRP(Material Requirement Planning) 자재 소요량계획 : 생산계획을 수행하는데 있어서 부품, 반조립품, 제료 등 필요한 것을 필요한 시기에 필요한 만큼 생산하는 계획 (최근 합리화된 생산시스템의 기본, 총 소요량 계산, 정밀소요량계산, 로트크기, 리드타임계산, 생산예산량 계산 등의 기능 보유)
제조실행시스템(MES)와 일맥상통
JIT (Just In Time)
주문이 들어오면 생산하는 시스템으로,
낭비를 철저히 배제, 필요없는 작업공정, 재고, 운반, 공정지연, 불량 등을 철저하게 제거 후 다른 공저응로 보냄, 생산성 증대
FMEA (Failure Mode and Effect Analysis)
신뢰성 방법론 분야에서 가장 흔히 사용되고 잘 알려진 정성적 신뢰성 방법론
시스템 변경이나 부품변경시 설계단계에서 수행하는 예방 차원의 신뢰성 방법론
목적 : 신뢰성 평가의 최적 기준을 달성하기 위해 경험적인 관점에서 부품을 분석하고 변경
신뢰성 측면에서 문제가 없는 척도가 RPN(Risk Priority Number, 위험우선순위)다.
rpn은 심각도, 발생도, 검출도의 곱으로 나타내진다
기본 아이디어는 제품의 시스템, 서브시스템 또는 부품의 발생 가능한 모든 고장 모드를 결정하는 것. 잠재적인 고장모드, 잠재적인 고장 영향, 잠재적인 고장원인을 파악하는 것 (이를 통해 고장을 사전에 파악하고 예방, ㅍ위험관리 및 품질 증대 )
제품 설계단계, 완료단계까지의 결함 발생 및 수정사항 작성, 그에 따른 고장 검출 및 예방방법 작성, 위험우선 순위도 작성 (고장 심각도, 발생빈도, 검출도 기준), 위험순위가 높은 항목부터 개선 및 조치
단계 - 파트 - 잠재고장 - 고장영향 - 심각도 - 고장 원인 - 발생도 - 관리방법 - 검출도(현재의 관리방법으로 발생할 정도) - RPN - 조치결과
흐름 : FMEA 게획 및 준비 -> 제품 분석 -> 기능 분석 -> 고장분석 -> 위험분석 -> 개선 및 최적화 -> 결과 공유
공정 PFMEA, 설계 DFMEA가 있음
PFMEA (+Process)
공정에 관한 FMEA
풀 프루핑 (fool proofing)
풀프루프(Fool Proof)란 표준작업, 기계의 위험성 등을 이해하지 못한 사람이 어떤 조작을 실수하지 않도록 하는 시스템 (실수하고 싶어도 실수할 수 없도록 하거나 실수가 있더라도 경보를 통해 작업자가 인지할 수 있도록 하는 시스템)
가드 풀프루프, 록기구 풀프루프, 트립기구풀프루프, 오버런기구 풀프루프, 밀어내기 풀프루프, 가동 방지 기구
가드 풀프루프(손이 위험 영역에 들어가지 않도록 설계하거나 들어가면 경보를 울림), 록기구 풀프루프(인터락; 2개 이상의 부분이 상호구속되거나, 열쇠를 이용 한쪽을 잠그지 않으면 다른 쪽이 열리지 않음), 트립기구풀프루프(신체 일부가 위험영역에 들어가면 기계가 작동하지 않고 정지 ,혹은 역전복귀함), 오버런기구 풀프루프(스위치를 끈 후 관성운동, 잔류 전류 검출하여 해당 기계가 완전히 정지하지 않으면 가드가 열리지 않음), 밀어내기 풀프루프(가드 자동부분이 열렸을때 신체를 밀어냄), 가동 방지기구(안전블록, 제어 회로, 레버락 등) 등이 있음
페일세이프(fail safe) : 기계 또는 시스템이 고장이 발생해도 피해가 확대되지 않고 단순 고장이나 일시적 운영이 계속되도록 하여 안전을 확보하는 설계방법, 기계 또는 시스템이 고장이 나더라도 비상장치나 다른 부품이 작동하여 사고를 예방하는 설계원리. 병렬부품을 이용
욕조곡선 (bath-tub curve) : DFR, CFR, IFR
사용중 일반적으로 나타나는 고장률을 시간의 함수로 나타낸 곡선
고장패턴은 크게 세가지 (DFR; Decreasing Failure Rate, 감소고장률) (CFR; Constant Failure Rate, 상수고장률), (IFRl Increasing Failure Rate, 증가고장률)이 있고 기타고장률(BTR; Bath-Tub failure Rate)등이 있음
초기고장, 우발고장, 마모고장이 있음
초기고장 : 설계나 제조상의 결함, 품질문제, 불량부품 혹은 사용조건, 환경의 부적합에 의해 초기 스트레스를 견디지 못해 고장 발생. 고장률은 점차 감소하는 경향 (설계, 원자재, 가공, 조립, 사용오류에서 기인하는 결함) , 대책은 디버깅, 시운전 중 하드웨어 결함을 찾는(초기고장기간의 제품을 시험 검사 고품분석을 실시) 번-인을 실시, 절저한 품질관리
우발고장 : 시간의 경과와 더불어 제품이 안정화되면서 사용조건의 우발적인 변화에 기인. 고장이 언제 발생하는지는 모르지만 항상 일정함, 근본적 개선은 설계 변경 필요, 정기적인 사용자 교육과 예방점검이 대책
마모고장 : 일정시간이 경과된 이후 마모 또는 노후에 기인하여 시스템 또는 설비의 고장률이 증가. 사전 검사나 감시에 의해 예지할 수 있는 고장. 신뢰성. 기계 자체 수명과 직결, 대책은 고장시 보수하는 사후보전, 시간에 따라 주기적으로 보수한ㄴ 예방보전, 상태에 따라 선제적으로 보수하는 예지보전이 필요함
폭포수 모델, 반복적모델, 프로토타입모델
폭포수 모델 : 요구사항분석, 설계, 구현, 시험, 유지보수 과정을 순차적으로 접근(널리 사용), 순차적으로 진행되어야하고 각 단계 결과물의 명확한 정의 필요
반복적 모델 : 사용자의 요구사항 일부분, 제품의 일부분을 반복적으로 개발하여 최종 시스템으로 완성하는 모델 (waterfall + prototyping), 증분개발모델과 진화적 개발모델이 있음
프로토타입모델 : 개발하려는 시스템의 주요 기능을 개발 초기에 모형을 만들어 평가 후 전체 시스템으로 확장하여 구현. 사전에 검토할 수 있으므로 불필요한 인력 자원의 낭비를 피할 수 있음
QDM금형 (QuickDelivey Mold)
단기간에 납기, 납품할 수 있는 금형
시작금형, 시금형, 간이금형
적은 수량을 생산할 수 있기 떄문에 시장성 확인을 위해 도입할 수 있음
장점 : 빠른 금형 제작기간, 저렴한 금형 제작 비용 (알루미늄과 같은 제작비용이 저렴한 소재), 초기시간과 비용투자가 적음
단점 : 코어의 크기가 정해져 있음 (코어의 크기를 넘어서는 제품은 이용할 수 없음), 코어가 견딜 수 있는 일정 수준을 넘어서면 사출 품질이 떨어짐. 금형의 정밀도가 떨어짐 (단단한 소재가 아니라서 정교하게 다듬을 수 없음)
무접점시퀀스, 유접점 시퀀스
유접점시퀀스 : 제어회로에 사용하는 소자, 유접점 릴레이를 이용, 릴레이 시퀀스
기계적 가동접점이 전자석에 의해 동작, 통전 또는 단전, 단순하고 저렴하나 수명의 한계점과 프록램 변경이 곤란함.
유접점 시퀀스의 장점 : 개폐부하 용량이 크고 과부하에 잘견딤, 전기적 잡음에 안정적, 온도특성이 양호. 단점은 접점이 마모되어 수명에 한계< 동작속도가 느리고 소비전력이 비교적 크며 진동충격에 약하고 외형이 큼
무접점 시퀀스 : 반도체 스위칭 소자를 이용한 무접점 릴레이에 의해 구성되는 시쿠너스. 트렌지스터, 다이오드, IC등의 반도체 스위칭 소자를 사용. 전압레벨의 고저나 신호의 유무로 대응. And, Or, Not 등 논리회로를 구현
장점은 동작속도가 빠르고 수명이 길고 진동충격에 강하고 소형화, 소비전력이 작음. 단점은 전기적 노이즈에 약하고 증폭회로가 필요하고 온도 변화에 약하고 동작상태 확인이 어려움
제조물책임(Product liability)
제조물책임법은 제조되어 시장에 나온 상품의 결함으로 인하여 3자의 생명, 신체나 재산에 피해가 발생한 경우 제조자 등 제조물의 생산, 판매 과정에 관여한 자의 과실유무에 상관 없이 제조자 등이 그러한 손해에 대하여 책임을 지도록 하는 법리.
과실책임 : 보증책임, 엄격책임과 함께 소송원인이 되는 책임 중 하나. 주의 의무 위반이 있을때 과실로 판단. 주의 의무 위반에는 피해를 예견해야할 예견의무, 피해의 결과를 회피하여야할 결과회피의무가 있음
보증책임 : 명시의 보증과 묵시의 보증으로 구분. 묵시의 보증은 상품 적합성에 따른 보증과 특정 목적 적합성에 따른 보증으로 구분
제조 vs 생산
제조(Manufacturing)은 기계류의 도움을 받아 원자재를 준비 용품(중간재)으로 전환하는 과정이고 생산(Production)은 원재료나 반제품과 같은 투입물을 가공물이나 서비스로 변환하여 기계를 사용하거나 사용하지 않을 수 있는 공정이나 방법
제조는 입력이 대규모의 산춞물로 변환되는 산업 부문에서 사용, 투입물 : 원자재, 부품의 형태
생산은 유용성을 창출하는 물질과 비물질 투입물을 생산물로 전환시키는 활동 (어떠한 과정을 거쳐서 결과를 만들어내는 모든 행위), 아이디어, 정보, 기술, 예술, 재능, 완성품 등 포함
제조는 항상 유형의 결과를 도출하고 생산은 유형 또는 무형의 결과를 도출
제조 <<< 생산 (모든 유형의 제조는 생산에 사용되지만 생산은 반드시 제조가 될 수 없음)
제조는 유형의 것, 생산은 무형의 산출물
가상공학
모든 제품개발 활동에서 실물모형이 사용되는 부분을 가상모형과 시물레이션으로 대체하고 정보를 통합 운용할 수 있도록 지원하는 기술 (모델링, 시뮬레이션)
특징 : 지능화(컴퓨터가 지능화), 분산처리 및 개방화, 편재화
DFA(조립성을 고려한 설계, Design for Assembly )
DFA는 제품의 설계를 조립하기 쉽게 만드는 방법론. 설계 단계에서부터 조립의 용이성을 고려하여 설계함으로써 조립 시간을 줄이고, 조립 오류를 줄이며, 조립 비용을 절감할 수 있음. DFA는 주로 부품 수를 줄이고, 조립 과정의 복잡성을 최소화하는 데 중점
DFM(Design for Manufacturing)
DFM은 제품을 제조하기 쉽게 만드는 설계 방법. 설계 단계에서 제조 공정을 고려하여 설계함으로써 제조 비용을 줄이고, 제조 품질을 향상시키며, 제조 시간을 단축할 수 있음. DFM은 주로 재료 선택, 공정 선택, 공정 능력 등을 고려하여 설계
DFMA(제조성 및 조립성을 고려한 설계)
FMA는 DFA와 DFM을 통합한 방법론으로, 제품을 제조하고 조립하기 쉽게 만드는 설계 방법론. DFMA는 제품 설계 초기 단계에서 제조 및 조립의 용이성을 동시에 고려함으로써 전체 비용을 절감하고, 제품 개발 시간을 단축하며, 품질을 향상시킬 수 있음. DFMA는 종종 제품의 라이프 사이클 비용을 최소화하는 데 초점을 맞춤
DFSS(식스시그마를 고려한 설계)
DFSS는 여섯 시그마의 원칙을 설계 단계에 적용하여 제품과 공정을 개선하는 방법론. DFSS는 주로 제품 설계 초기 단계에서부터 결함을 예방하고, 품질을 보장하며, 고객 요구 사항을 충족시키는 데 중점을 둠. DFSS는 통계적 도구와 기법을 사용하여 설계 품질을 향상시키고, 프로세스 변동을 줄이며, 제품 성능을 최적화.
All tool (양산금형 생산부품)
양산금형으로 시작라인 조건하 생산
Full Tool (양산공정 생산부품)
4M이 갖추어진 양산금형 및 양산라인의 정규 단위시간당 생산개수 조건하에 생산된 부품
ISIR(Initial Sample Inspection Report, 초도품 검사 보고서)
수요자의 설계사양 및 요구조건이 부품 공급자에게 정확히 이해되었는가를 확인하고 공급자의 공정이 제품요건을 만족시킬 수 있는가를 확인하는 업무. 실제 완성차 양산시 고객의 요구 품질을 만족시키기 위함
SOP(Start of Production, 양산시점)
양산시점, 모든 제조업은 SOP를 마지막 이벤트로 달려간다
IRE(Initial Risk Evaluation, 부품 초기위험도평가)
제품 개발 초기 단계에서 각 부품이나 공정에 내재된 잠재적 위험 요소를 평가하는 과정임. IRE는 제품의 품질, 안전성 및 신뢰성을 보장하기 위해 중요한 역할을 하며, 주로 다음과 같은 목적을 가지고 수행함:
1. 위험 요소 식별
각 부품이나 공정에 내재된 잠재적 위험 요소를 식별함. 이는 고장 모드, 잠재적 결함, 안전 문제 등을 포함함.
2. 위험도 평가
식별된 위험 요소의 심각도, 발생 가능성, 검출 가능성을 평가함. 이를 통해 각 위험 요소의 전반적인 위험도를 산출함.
3. 우선순위 설정
평가된 위험도를 기반으로, 해결해야 할 위험 요소의 우선순위를 설정함. 이는 자원을 효과적으로 할당하고, 중요한 문제를 먼저 해결하는 데 도움이 됨.
4. 대응 계획 수립
각 위험 요소에 대한 대응 계획을 수립함. 이는 설계 변경, 추가 시험, 품질 관리 강화 등을 포함함.
5. 추적 및 검토
IRE 과정에서 식별된 위험 요소와 대응 계획을 지속적으로 추적하고 검토함. 이는 제품 개발 과정에서 발생할 수 있는 새로운 위험 요소를 신속하게 식별하고 대응할 수 있도록 함.
PPAP(Production Part Approval Process, 생산부품승인절차)
자동차 부품 개발 과정이 양산 전에 부품의 성능 및 시험항목 등에 대하여 완성차로부터 받는 승인 절차, ISIR과 동일의미,
'Mechanical Engineering Study > 공정설계' 카테고리의 다른 글
제조물 책임법, PL(Product Liability)법, 제조물책임법 고려사항 (1) | 2024.11.22 |
---|---|
공정설계 고려 사항 : 자본집약도 (capital intensity), 자원유연성 (resource flexibility), 수직적 통합 (vertical integration), 고객 참여 (customer involvement) (2) | 2024.11.19 |
가치공학(VE; Value Engineering) (0) | 2024.06.28 |
생산라인, 공장 레이아웃 (Lay out) 설계, 공자 기계 배치 방법, 공정별 배치, 제품별 배치, 셀룰러 배치 (0) | 2024.06.21 |
시방서, 기술사양서, 요구사양도 (specification) (0) | 2024.06.11 |