1. 개요
1) 위험성 평가 정의
유해, 위험 요인을 파악하여 위험성의 정도를 결정하는 일련의 과정 위험성을 낮추기 위한 적절한 조치를 위해 시행.
사업주와 근로자가 주체가 되어, 안전보건관리책임자, 관리감독자, 안전관리자, 보건관리자, 안전보건담당자 등이 참여하여 각 역할 분담 후 위험요인을 찾아내게 됨
정성적 위험성 평가 기법중 가장 널리 알려진 방법으로, 공장 및 플랜트 혹은 설비에 대하여 위험성과 운정성을 정해진 규칙과 설계도면을 바탕으로 체계적 분석 및 평가하는 방법
정성적 평가 방법 (FMEA, PHA, Checklist, HAZOP)
정량적 평가 방법 (ETA, FTA, CA, CCA, MORT, THERP)
2) 위험성 평가의 일반적인 절차
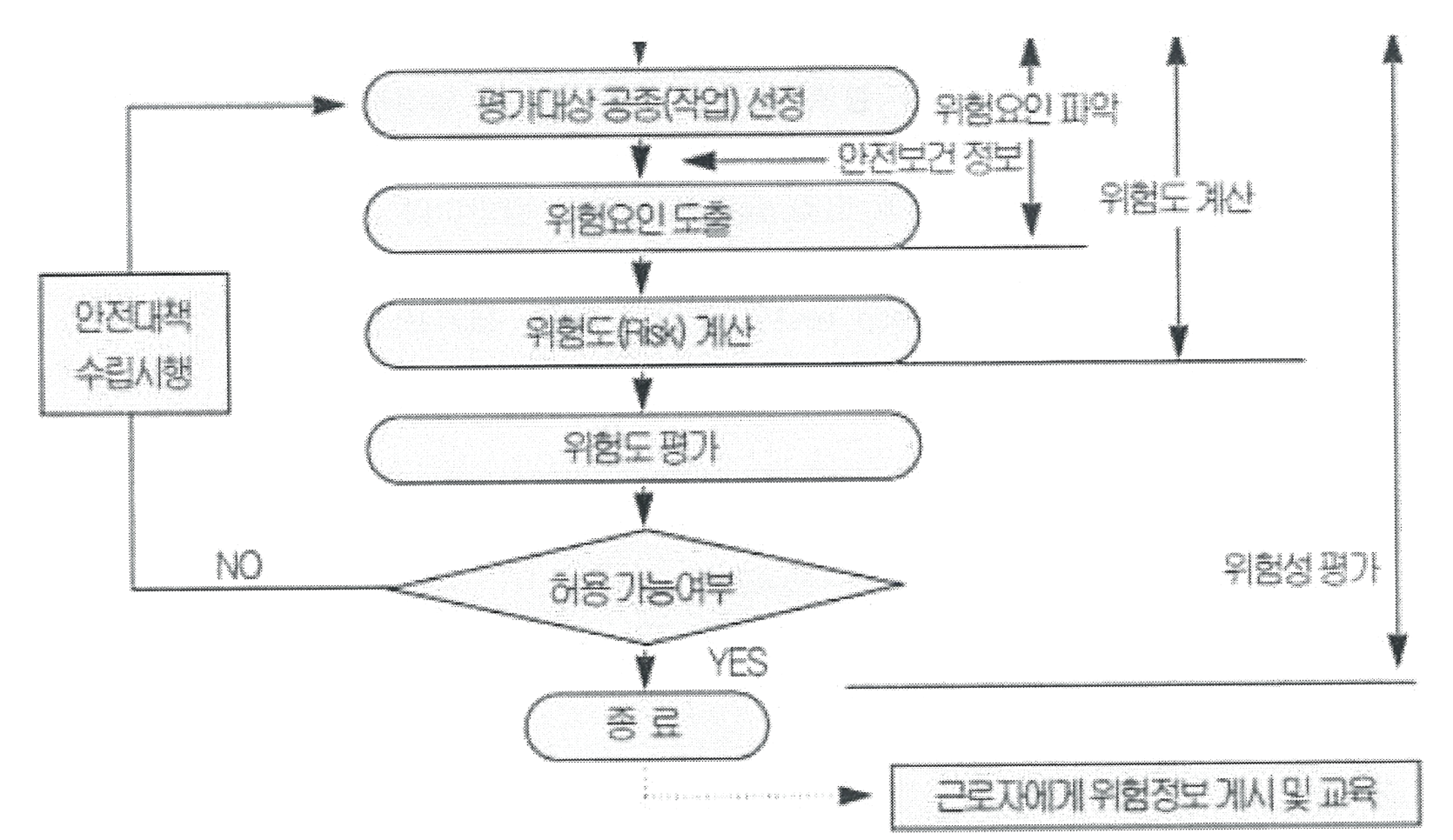
(1) 위험성 평가 및 대책 실시단계
1단계 : 위험요인 확인
작업 장비 사용으로 발생할 수 있는 위험요인을 확인해야 한다.
2단계 : 위험성 추정 및 위험성 평가
사고 위험성은 "손상 심각도" 와 "손상 확률'’ 의 요소를 기본으로 결정한다.
3단계 : 대책 선정 및 조치
대책은 반드시 가능한 최대 범위 내에서 위험요인 제거 또는 적어도 최소화를 목표로 해야 하며 이것이 가능하지 않다면 적절한 방호 장치를 반드시 두어야 한다. 가능한 모든 잔존 위험요인은 반드시 사람과 관련된 대책(교육, 개인보호구, 지침)으로 해결해야 한다.
(2) 사업주의 역할
사업주는 제조자의 위험요인 분석을 반복하거나 입증하는 것(지침 2006/42/EC에 의거)이 아니 명시된 위험요인으로 인해 기계류/작업 장비로 작업하는 근로자에게 발생하는 잔존 위험성 수준을 확인하고 특별한 대책으로 이런 위험성을 통제해야 한다.
- 기계류 또는 작업 장비 사용과 관련한 기존 관련 규칙 및 지침
- 잔존 위험성에 대한 정보와 더불어 기계류에 대한 제조자 지침
- 작업 사고 및 직업병 기록
- 위험요인에 대한 근로자의 지식 및 경험
- 작업장 특수 조건
위험요인 확인은 기계류/작업 장비의 조립, 설치, 설정 및 조정, 운영, 유지보수, 분해 및 폐기등 모든 수명 주기 단계를 포함해야 한다.
3) 위험성 평가 종류
- HAZOP
- FMEA
- FTA
항목 | HAZOP | FMEA | FTA |
개념 | 운영상 위험 요소 사전 파악 | 영향 해석, 해당 부품 도출 | 사고 원인 연역적 분석 |
목적 | 위험 요소 및 조업상 문제점 파악 | 영향도 도출, 전개, 고장감소 방안 제시 | 장치이상, 작업자 실수 조합 발견 |
특징 | 가이드워드 사용, 편차 연관 위험 탐색 | 상향식 기법, 개선책 검토 | 논리 회로 기반 트리구조, 정량평가 |
객관성 | 정성적 | 정성적 | 정량적 |
산출물 | 위험성 평가 결과 및 조치 계획서 | FMEA 결과물, 잠재고장 영향 분석 | FTA트리, 최소 cut set, pass set |
장점 | 브레인스토밍, 리더의 체계적인 진행 가능 | 비교적 쉽고 빠른 결과 도출 | 객관적, 정량화 결과 도출 |
단점 | 팀 단위의 다수 인원 필요 | 작성자의 주관적 의견 ㅏㅂㄴ영 | 시간, 경비의 과다 필요 전문가 필수 |
2. HAZOP
1) HAZOP(Hazard and Operability) 정의
HAZOP은 시스템의 위험성과 운전 가능성을 평가하는 체계적인 방법론.
공정에 존재하는 위험요인과 공정의 효율을 떨어뜨릴 수 있는 운전상 문제점을 찾아 원인을 제거
2) HAZOP 수행 방법
- TEAM 구성
리더, 기록원, 엔지니어 등으로 팀을 구성 - 스터디 노드 선정
공정, 시스템 별 검증 필요한 요소를 분리하여 각각 평가하기 위해 Node를 설정한다 - 위험도 평가
- 원인을 검토하고 기록 (주로 브레인스토밍 방식으로 진행)
- 결과 : 원인에 따른 예상 결과를 기록
- 안전 조치 현황 : 각각 예상되는 결과를 방지하기 위해 안전장치가 어떻게 반영되어잇는지 기록
(fail safe, fool proof 등) - Risk Ranking 도출
위험 빈도와 위험의 영향도를 고려하여 등급을 매김 (FMEA의 원리와 비슷)
영향도는 인명손실, 경제적 피해 등을 종합적으로 고려함 - 권고사항 작성
추가 조치가 필요할시 안전설비나 대책을 기록함
3. FMEA
1) FMEA (Failure Mode Effect Analysis) 정의
FMEA는 시스템적 방법으로 시스템, 서브시스템 혹은 부품에 발생 가능한 모든 고장 모드를 결정하는 것
이와 동시에, 가능한 고장 영향 및 고장 원인이 제시됨
고장형태영향분석, FMEA, PFMEA, DFMEA
22-2-4 PFMEA(Process Failure Mode and Effects Analysis)와 관련하여 ① 분석은 언제 실시하며, ② 분석을 하는 이유는 무엇이고, ③ PFMEA를 통해서 얻을 수 있는 것은 무엇인지 설명하시오.19-4-2 FMEA(failure mode ef
romanticdeer.tistory.com
4. FTA (Fault Tree Analysis)
1) FTA(결함수분석) 정의
어떤 고장 혹은 이탈을 트리 구조로 정리하여 해석
시스템 고장 혹은 사고를 발생시키는 원인들과의 관계를 논리기호를 통해 트리구조로 만들고, 이에 의거하여 시스템의 고장 확률을 구해 고장이 발생할 수 있는 취약부분을 찾아내 시스템의 신뢰도를 개선하는 방법론
TA는 부울 논리를 사용하여 시스템을 분석하고 실패의 원인으로 이어지는 경로를 찾고, FTA는 상단의 단일 지점에서 시작하여 하향식 접근 방식을 사용하여 시스템의 상태를 확인함.
FTA는 논리적 기호를 사용하여 시스템의 하위 수준에서 기본 이벤트를 확인하고 시스템 수준의 실패 원인을 식별함. 고장 트리 다이어그램은 논리 게이트와 이벤트를 사용하여 실패 체인을 나타내고, 이벤트를 참/거짓 진술로 테스트하고 이를 연결하여 실패의 근본 원인을 파악
고장 트리 다이어그램은 논리 게이트를 사용하여 시스템 내 기본 이벤트의 상태를 확인하여 시스템의 상태를 나타내며, 방법으로는 주요 이벤트를 상단에 배치하고 그 원인을 나타내는 분기를 그림. 각 분기는 즉각적인 원인을 나타내는 분기로 다시 나뉘며, 이러한 논리는 시스템의 최하위 수준까지 계속 반복 실시함
2) FTA 방법
예를 들어, A라는 고장이 있다고 가정하면,
A고장이 발생하기 위한 조건을 그 아래에 적어야함 (분기를 시켜서)
A고장이 발생하기 위해서 a원인, b원인이 동시에 발생해야지 고장이 나는 조건이라면, and 논리게이트를 이용하여 표기함
이후, 이 두 and 조건을 만족하면 사고 (accident)가 발생하는 원리
해당 방식은 간단하게 해당 고장 확률을 정량적으로 표현할 수 있는데,
a원인이 발생할 확률이 0.001%/year, b원인이 발생할 확률이 0.02%/year이라면, A고장이 발생할 확률은 and조건에 따라 0.001 x 0.02%/year로, 1년에 0.0000002번 나타나는 고장이 되는 것
cut set
주어진 기본 사건의 조합이 계통 기능을 상실시키는 경우 이 사건들의 조합을 cut set이라 표현
시스템 안전, Fail Safe, Fool Proof, Temper Proof
1. 풀프루프(Fool Proof)설계 1) 풀프루프 정의 (오조작 방지 장치)모든 인간은 누구나 실수를 하며, 실수는 심각한 안전사고로 이어질 가능성이 존재한다 따라서, 오퍼레이터(operator) 혹은 근로자가
romanticdeer.tistory.com
제조물 책임법, PL(Product Liability)법, 제조물책임법 고려사항
1. 개요 1) 제조물 책임법(PL법) 정의 제 1조(목적) 법은 제조물의 결함으로 발생한 손해에 대한 제조업자 등의 손해배상책임을 규정함으로써 피해자 보호를 도모하고 국민생활의 안전 향상과
romanticdeer.tistory.com
공정설계 고려 사항 : 자본집약도 (capital intensity), 자원유연성 (resource flexibility), 수직적 통합 (vert
24-2-6 공정설계의 의미와 공정설계를 위한 고려사항 중 자본집약도 (capital intensity), 자원유연성 (resource flexibility), 수직적 통합 (vertical integration), 고객 참여 (customer involvement)에 대하여 설명하시오
romanticdeer.tistory.com
공정설계, 품질, 제조업 관련 용어 정리
1. 용어 정리 1) 공정설계 관련 용어 공정설계 (Process Engineering, Process Design)제조공정설계는 제품을 생산하고자 할 때 그 제품의 제조과정, 즉 공정(Process)에 관한 것으로, 원자재를 이용하여 도
romanticdeer.tistory.com
생산계획 (Production Planning), 생산 능력, 생산 적합성 판단, 가동률, 생산 능력 측정, 생산 관리
23-4-6 공정설계에 있어서 생산 적합성 판단과 관련하여 다음을 설명하시오. (a. 생산능력의 정의와 중요성 b. 생산관련 의사결정에서 고려사항 c. 생산능력 측정의 목적과 효과 d. 생산능력 측정지
romanticdeer.tistory.com
공정설계 (Process Design)
23-4-6 공정설계에 있어서 생산 적합성 판단과 관련하여 다음을 설명하시오. (a. 생산능력의 정의와 중요성 b. 생산관련 의사결정에서 고려사항 c. 생산능력 측정의 목적과 효과 d. 생산능력 측정지
romanticdeer.tistory.com
최적설계 (Optimum Design)
23-1-12 최적설계 제품을 생산하는데 고려하고, 확인해야 할 요소에 대하여 설명하시오.23-3-3 최근의 공작기계는 고속화, 고정밀화, 복합화에 초점을 맞춰 개발되고 있는 추세이다.
romanticdeer.tistory.com
'Mechanical Engineering Study > 공정설계' 카테고리의 다른 글
고장형태영향분석, FMEA, PFMEA, DFMEA (1) | 2024.12.09 |
---|---|
시스템 안전, Fail Safe, Fool Proof, Temper Proof (5) | 2024.12.05 |
제조물 책임법, PL(Product Liability)법, 제조물책임법 고려사항 (1) | 2024.11.22 |
공정설계 고려 사항 : 자본집약도 (capital intensity), 자원유연성 (resource flexibility), 수직적 통합 (vertical integration), 고객 참여 (customer involvement) (2) | 2024.11.19 |
공정설계, 품질, 제조업 관련 용어 정리 (4) | 2024.10.25 |