Contents
- <구분>
- <기출>
- 1. 개요
- 1) 압연가공 정의
- 2) 압연 조건 (압연이 이루어지기 위한 조건)
- 3) 압하율
- (1) 압하율을 높이기 위한 방법
- (2) 일반적인 압하율
- 4) 압연력 분포도 (friction hill)
- 5) 압연 작업에 영향을 미치는 요소
- 2. 압연공정 구분 (온도에 따른 구분)
- 1) 열간 압연
- 2) 냉간 압연
- 3) 열간압연강판, 냉간압연강판의 제조 공정
- 3. 압연 공정 구분 (제작 제품에 따른 구분)
- 1) 압연 공정의 구분
- 4. 압연 공정 구분 (롤러 개수 및 조합 형식에 따른 구분 )
- 1) 롤의 개수에 따른 구분
- (1) 2단 압연기
- (2) 3단 압연기
- (3) 4단압연기
- 4) 특수 압연기
- (1) 센지미어 압연기 (Sendzimir Mill)
- (2) 유니버셜 압연기 (만능 압연기)
- (3) 유성 압연기
- (4) 클러스터 압연기
- 5. 조질 압연
- 1) 조질 압연 개념, 뤼더스 밴드
- 6. 압연 공정의 결함
- 1) 표면 결함 (surface defect)
- 2) 구조적 결함
- 3) 라미네이션(Lamination), 라밀라 테어 결함
- 4) 줄무늬 결함
- 7. 압연 공정에 대한 고찰
- 1) 압연 롤의 조건
- 2) 제어 압연 냉각 (thermo-mechanical control process)
<구분>
- 압연가공
- 온도에 따른 구분
- 열간압연 (hot rolling)
- 냉간압연 (cold rolling)
- 제품에 따른 구분
- 섹션압연기
- 로드압연기
- 바압연기
- 시트압연기
- 분괴압연기
- 블룸
- 빌렛
- 슬래브
- 압연 롤러 개수 및 조합 형식에 따른 구분
- 2단식 압연기
- 비가역 2단 압연기
- 가역 2단 압연기
- 3단식 압연기
- 4단식 압연기
- 6연 압연기
- 특수 압연기
- 센지미어 압연기 (Sendzimir Mill)
- 유니버셜 압연기 (만능 압연기)
- 유성 압연기
- 2단식 압연기
- 조질압연 (Skin Pass Mill)
- 온도에 따른 구분
<기출>
- 기계 20-1-3 다음 소성가공에 대하여 설명하시오. 가. 압연가공 나. 압출가공 다. 인발가공 라. 프레스가공 마. 단조가공
- 기계 18-2-6 클러스터 압연기의 개략도를 그리고 이 압연기를 사용하는 이유에 대하여 설명하시오
- 기계 16-2-5 클러스터 압연기의 개략도를 그리고 이 압연기를 사용하는 이유를 설명하시오.
- 기계 13-2-2 압연공정에서 롤(roll)에 작용하는 압연력 분포도 (friction hill)를 그림으로 그리고, 설명하시오
- 기계 12-2-4 압연 작업에 영향을 미치는 요소 5가지를 설명하시오
- 금속 23-4-1 냉간압연(cold rolling)강판의 특성과 생산 공정에 대하여 설명하시오.
- 금속 23-4-6 금속재료 압연강판 제조에서 라미네이션과 용접시공에서 발생하는 라멜라 테어 결함에 대한 다음 물음에 답하시오. 1) 각 용어의 정의 및 특징에 대하여 설명하시오. 2) 라멜라 테어 발생 원인 및 방지대책에 대하여 설명하시오. 3) 라멜라 테어 품질관리 방법으로 기계시험 및 비파괴검사에 대하여 설명하시오.
- 금속 20-3-2 판재 압연 가공 시 재료가 압연 롤 안쪽으로 쉽게 물려 들어가기 위한 조건과 제품에 따른 압연 분류에 대하여 설명하시오.
- 금속 19-1-7 열간압연과 냉간압연의 특징을 쓰고, 관련 구분 기준에 대하여 설명하시오.
- 금속 19-2-2 조질 압연(Skin Pass Mill)에 대하여 정의하고, 그 목적을 설명하시오.
- 금속 19-2-5 압연공정에서 압하율을 증가시키는 방안을 설명하시오.
- 금속 18-4-3 압연공정의 제어목적은 판 두께 적중률을 향상시키고, 판의 wave 결함을 제거하는데 있다. 아래의 물음에 답하시오. (1) 판 두께에 영향을 미치는 인자들을 설명하시오. (2) 길이방향의 판 두께를 제어하기 위해 롤 간극을 조정하는데, 압연기의 탄성곡선과 소재의 변형에 따른 소성곡선의 관계를 이용하여 설명하시오. (3) 판의 폭 방향 두께와 wave 결함을 제어하기 위한 방법을 설명하시오.
- 금속 17-4-5 압연공정에서 결함을 원인별로 구분하고 특징 및 대책을 설명하시오.
- 금속 16-2-6 압연가공에서 압연조건과 압하율에 대하여 설명하시오.
- 금속 15-2-4 압연공정(Rolling) 에서 압하율을 크게 하는 요소 중 3가지만 설명하시오
- 금속 14-4-4 저탄소강판의 조질압연 시 줄무늬 변형이 발생하였을 때 이에 대한 원인과 대책을 설명하시오
1. 개요
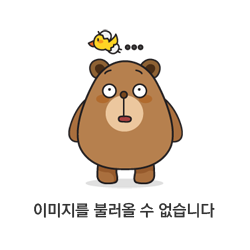
1) 압연가공 정의
회전하는 한 쌍의 롤러(roller) 사이로 재료를 통과시키며 압축하중을 가하며
1) 두께를 줄이고 2) 단면의 형상을 변형시켜 3) 각종 판재, 봉재, 단면재를 생산하는 가공법
(금속제품의 약 90%가 압연가공을 통해 만들어짐)
압연가공시 소재의 온도에 따라 (재결정온도 이상인지 이하인지) 열간압연과 냉간압연으로 구분할 수 있음
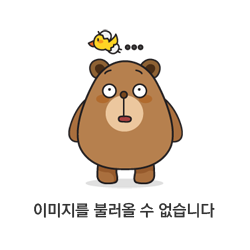
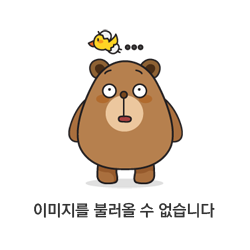
2) 압연 조건 (압연이 이루어지기 위한 조건)
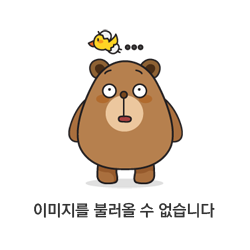
- 회전하는 롤과 소재의 접촉각(물림각)을 a
- 롤로부터 소재가 받는 힘을 P
- 소재와 롤 사이의 마찰계수를 μ
- 소재와 롤 사이 마찰력 μP
- 이때 Psin(a)는 소재를 밀어내는 힘이고, μPcos(a)는 소재를 롤로 끌어들이는 힘이기 떄문에 μPcos(a) ≥ Psin(a)여야 함
따라서 μ ≥ tan a 일때 소재가 자력으로 롤 사이로 물려 들어간다
마찰계수 μ는 열간압연일때 0.1 ~ 0.3이고 냉간압연일때 0.05 ~ 0.1정도임
3) 압하율
압하량은 압연에 의한 변형 정도 (압연 전후의 두께차) H0 - H1
압하율은 압하량을 압연 전 두께로 나눈 값 (H0 - H1) / H0 x 100(%)
동일 압하율의 경우 마찰계수가 클수록 소재의 폭 증가는 커지고 소요압연동력또한 커짐
냉간압연의 경우 마찰계수가 클수록 결함 (균열, 가장자리 갈라짐)이 쉽고 열간압연의 경우 가는 균열이 표면에 생기기 쉬움
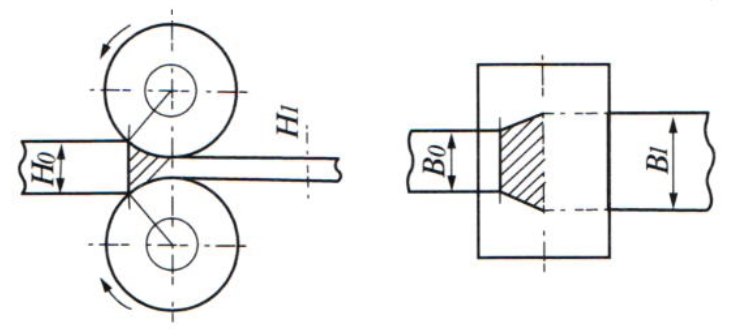
(1) 압하율을 높이기 위한 방법
- 지름이 큰 롤러를 사용 (롤 직경이 커야함)
- 롤러의 회전속도를 낮춤
- 소재의 온도를 높게 함
- 압연재를 뒤에서 밀어줌
- 마찰계수가 높을수록 압하율이 증대함
: 롤 표면에 홈을 만들거나, 모래를 뿌리거나, 가성소다액을 부어 롤면을 탈지하기도 함
(2) 일반적인 압하율
- 열간압연 압하율은 냉간압연의 압하율보다 크며, 30 ~ 45%가 보통 (50 ~ 60%도 있음)
- 냉간압연의 강판의 경우 최초와 최후의 압하율이 10% 전후이고 도중에는 30%정도 됨
- 황동 등은 10~20%가 일반적임
4) 압연력 분포도 (friction hill)
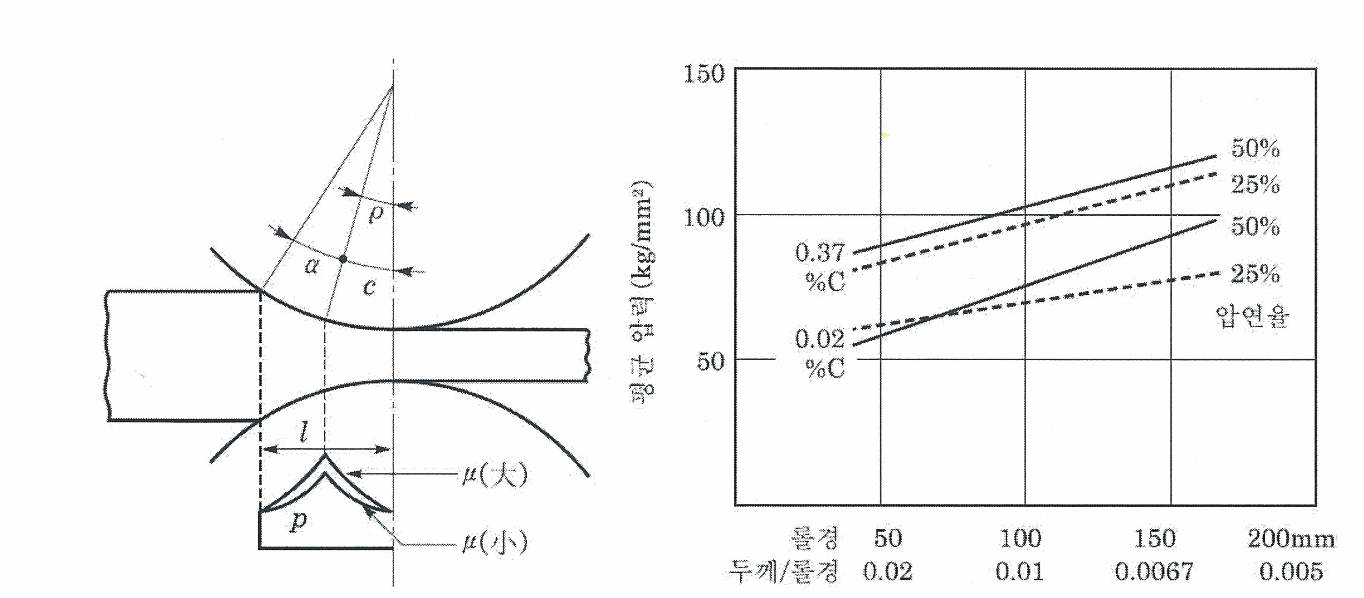
- 접촉면에서 압력 분포는 압연재의 폭 방향에서는 중앙부가 가장 높음 (양단으로 갈수록 압력이 감소)
- 압연방향으로는 중립점에서 가장 압력이 높고 양쪽으로 갈수록 감소함
- μ가 클수록 최대 압력 또한 커짐
5) 압연 작업에 영향을 미치는 요소
재료의 두께와 압하량이 같을 경우, 롤의 반경 R을 작게 하면 압연하중 P가 작아지고 압연토크 M이 작아져 압연하기 쉬워진다
(이러한 이유에서 실제로 압연을 행하는 잡업롤의 직경을 작게 설계함)
압하율이 클수록 공정수가 줄어서 경제적이지만 과대하면 재료에 홈이 생길 수 있음
- 압연 속도
압연속도가 빨라지면 마찰계수가 작아져 압연력 P가 작아져 고속ㅇ에서 얇은 판 제작이 용이함 - 압연 온도
압연온도가 증가함에 따라 압하율이 증가함 - 마찰 계수
마찰계수가 크면 압하율을 증가시킬 수 있음
2. 압연공정 구분 (온도에 따른 구분)
재결정 (recrystallization), 재결정온도, 냉간가공, 열간가공
22-1-3 금속의 열처리과정 중 발생하는 재결정에 대하여 설명하시오 13-1-4- 소성가공에서 열간가공(hot working)과 냉간가공(cold working)의 특징을 비교하여 설명하시오 금속 22-1-13 열간압출법(hot extrusi
romanticdeer.tistory.com
1) 열간 압연
"재결정 온도 이상에서 가공"하는 압연공정
장점) 변형저항이 적어 동력소모가 적고, 짧은 시간에 강력한 가공이 가능
단점) 소재 표면에 산화피막이 생기고, 냉각되면서 수축이 되어 표면 정밀도가 떨어짐(정밀가공에 부적합)
(1) 열간압연강판 (SPHC)
- 가공이 쉬움
- 표면에 산화가 발생
- 얇은 철판, 아연 도금 강판, 주석 도금 강
재료 | 온도범위 (도) |
연강 | 800~1180 |
특수강 | 850~1150 |
구리 | 650~950 |
두랄루민 | 360~440 |
알루미늄 | 300~520 |
Y합금 | 360~460 |
2) 냉간 압연
재결정 온도 이하에서 가공
장점) 가공표면이 깨끗하고 정확한 치수로 가공할 수 있음
단점) 변형저항이 커서 동력의 소모가 크고 가공경화가 발생해 기계적 성질(강도, 경도)가 증대됨
주로 박판가공이나 비철금속의 완성가공에 이용됨
(1) 냉간압연강판 (SPCC)
(강괴로부터 열간압연 후 냉간압연, 풀림처리 및 조질압연을 통해 제작됨)
- 프레스 성형 품질이 우수
- 표면이 미려
- 치수가 정확
3) 열간압연강판, 냉간압연강판의 제조 공정
열간압연강판
슬래브 가열 → 조압연 → 사상압연 → 냉각 및 권취
냉간압연강판
열간압연 → 산세(스케일 제거) → 냉간압연 → 표면청정 → 소둔(응력제거열처리) → 조질압연 → 정정
2024.03.03 - [Mechanical Engineering Study/소성가공] - 압연 - 열간압연강판 / 냉간압연강판 제조 공정
3. 압연 공정 구분 (제작 제품에 따른 구분)
1) 압연 공정의 구분
압연은 블룸, 빌렛, 슬래브 등을 만드는 1차가공(분괴압연)과 이 중간재로 각종 판재, 봉재, 레일과 같은 단면제와 포일(foil)을 만드는 2차가공으로 분류됨
잉곳 → 블룸 → 빌렛 → I형 강, 홈 형강 등 최종 단면재
- 섹션압연기
- 로드압연기 (지름 12mm 이하의 긴 봉재)
- 바압연기 (지름 12 ~ 100mm 의 원형 또는 100 x 100mm 사각단면의 긴 봉재)
- 시트압연기 (폭 450mm 이상, 두께 0.75~15mm 정도의 코일 형태의 판재)
- 분괴압연기
- 블룸 (bloom, 250 x 250mm ~ 450 x 450mm 정도의 사각형 또는 정방형 단면재료)
- 빌렛 (billet, 40 x 40mm 사각형 단면 이상의 단면적을 갖는 굵은 봉재)
- 슬래브 (slab, 최소 폭 250mm, 두께 40mm 이상의 직사각형 단면 재료, 각종 판재, 봉재, 형상을 갖는 구조물 재료로 재압연)
4. 압연 공정 구분 (롤러 개수 및 조합 형식에 따른 구분 )
- 2단식 압연기
- 비가역 2단 압연기
- 가역 2단 압연기
- 3단식 압연기
- 4단식 압연기
- 다단 압연기
- 특수 압연기
- 센지미어 압연기 (Sendzimir Mill)
- 유니버셜 압연기 (만능 압연기)
- 유성 압연기
1) 롤의 개수에 따른 구분
(1) 2단 압연기
스캔들 내에 지름이 같은 2개의 롤이 상하에 있음
비가역식은 한쪽방향으로만 움직이기 떄문에 재료를 롤에 통과시켜 압연 후 다시 원래 위치로 운반하여 압연을 되풀이함
가역식은 반대로 롤러가 회전하여 원래 위치로 이동
(2) 3단 압연기
3단식, 서로 인접한 각 롤은 압연할때 반대 방향으로 회전, 대형 재료의 압연에 사용
(3) 4단압연기
지름이 작은 한 쌍의 작업 롤의 위 아래에 지름이 큰 롤을 받쳐주어 굽는 것을 방지하는 동시에 압연 동력이 적게 ㅂ라생
주로 냉간 압연기에 많이 사용됨
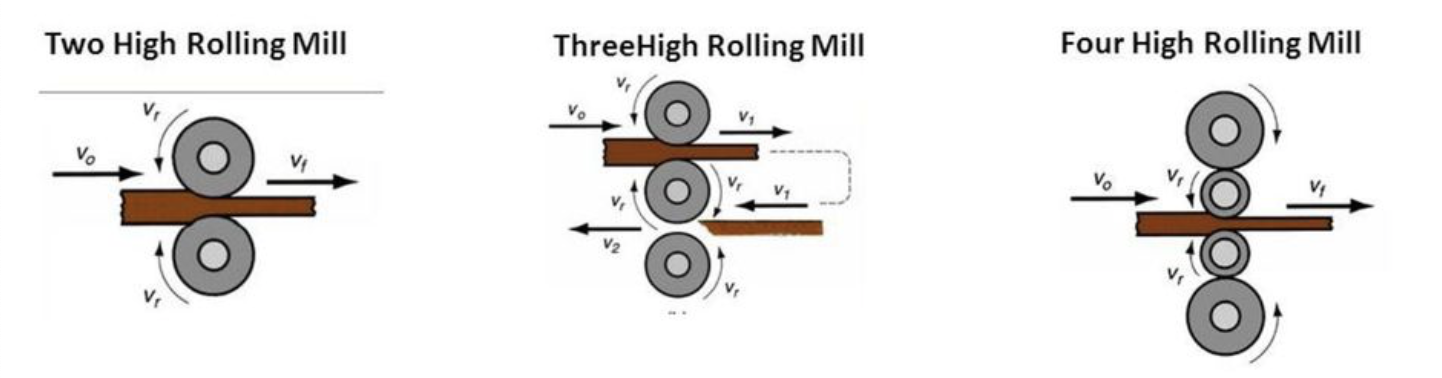
4) 특수 압연기
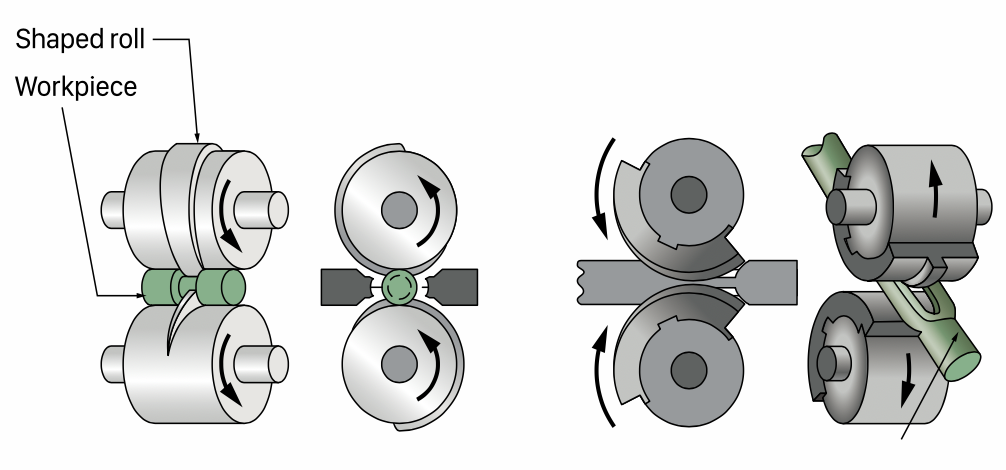
(1) 센지미어 압연기 (Sendzimir Mill)
판 두꼐의 밀도 및 공차가 엄격한 얇은 판의 압연에 사용 (냉간압연)
작업롤의 지름을 되도록 작게 한 것, 6단과 12단, 20단 등 3종류가 있음
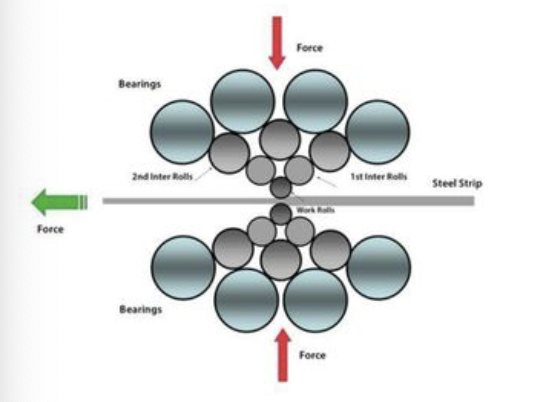
(2) 유니버셜 압연기 (만능 압연기)
수평롤과 수직롤로 조합되어 1회의 공정으로 재료의 두께와 너비를 동시에 압연
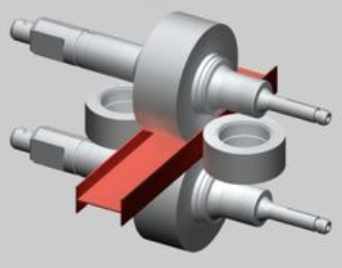
(3) 유성 압연기
지지롤 주변의 유성롤이 소재와 접촉하면서 가공하는 압연기
지름이 큰 받침롤 주위에 지름이 작은 작업롤을 많이 배치한 압연기
(4) 클러스터 압연기
클러스터압연기는 냉간압연으로, 얇은 판을 양산하는데 사용
Y형 압연기, 6단 압연기라고 하며, 작업 롤러 직경을 작게 하면 압연면이 더 많이 접촉하여 지지롤러의 효과를 높일 수 있기 때문에 (압연하기 쉬워지기 때문에) 박판 압연에 사용되며, cluster 압연기라고 함
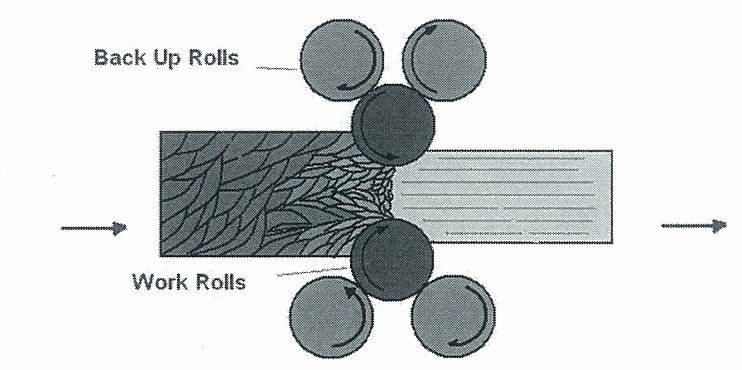
5. 조질 압연
1) 조질 압연 개념, 뤼더스 밴드
냉연강판은 냉간가공으로 인해 가공경화되어있기 때문에, 사용에 적합하도록 적절한 인성을 부여해야함
이를 위해 강판을 어닐링하여 내부 응력을 제거한 뒤, 결정립자를 세밀하게 하기 위해 가벼운 냉간압연을 하게 되는데 이를 조질압연이라고 함
소둔을 마친 코일의 기계적 성질 개선 / 표면 조도 개선 / 항목점 연신을 방지 (뤼더스 밴드 형성 방지)
2024.03.03 - [Mechanical Engineering Study/소성가공] - 압연 - 조질 압연, 뤼더스밴드, stretcher strain
6. 압연 공정의 결함
롤 사이에서의 불균일한 변형으로 인해 압연판에는 잔류응력이 발생할 수 있음
직경이 작은 롤을 사용하거나 압하율이 작으면 소재의 표면 부근에만 소성변형이 되어 표면에는 압축잔류응력을 남기고 가운데 부분은 인장 잔류응력을 남김 (숏피닝과 유사)
큰 직경의 롤을 사용하거나, 두께 감소율이 큰 경우에는 표면층 뿐 아니라 전반적인 부피변형이 발생하고, 롤과 소재간의 접촉부에서 표면 마찰로 인한 구속이 발생하여 반대방향으로 잔류응력이 생김 (표면 인장잔류응력, 가온데 압축잔류응력)
- 표면 결함
- 구조적 결함
- wave결함(좌굴, buckling)
- 균열
- 입벌림 (alligatoring)
- 라밀라테어 결함
- 줄무늬 결함 (뤼더스 밴드 형성)
1) 표면 결함 (surface defect)
재료 자체의 불순물, 스케일, 이물질 등으로 발생
열간압연시 압연가공 전 토치를 이용하여 스케일을 제거해야함
2) 구조적 결함
- 파도형 결함(wave edge)
롤러의 휨으로 인하여 판재의 가장자리가 중심부보다 얇게 가공되면서, 가장자리 길이가 길어져 나타나는 좌굴 현상
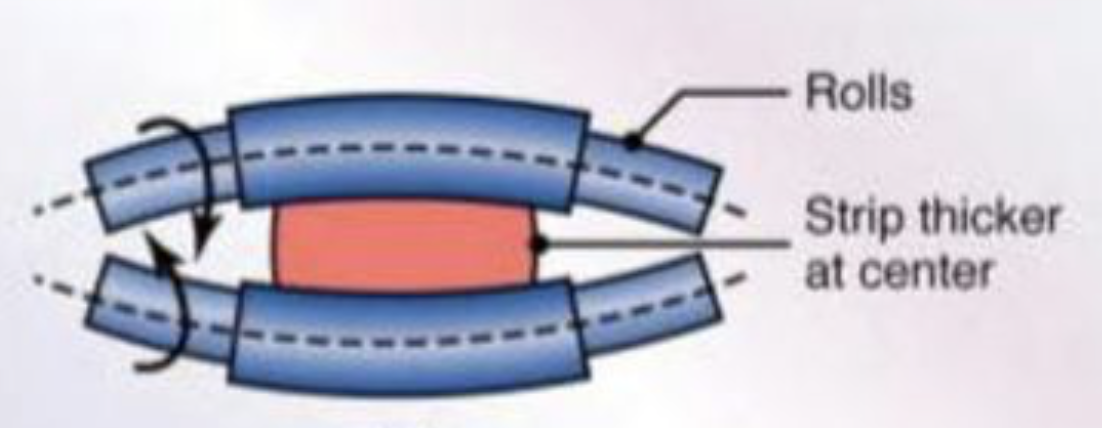
- 균열
압연 소재의 연성이 부족하거나, 롤의 배럴링 (barrelling)에 의해 발생함 - 입벌림 결함 (alligatoring)
소재로 사용되는 잉곳의 기공, 수축공 등 내부 결함에 의해 발생

3) 라미네이션(Lamination), 라밀라 테어 결함
라미네이션(Lamination)이란 압연 공정 중 강괴 내의 개재물이나 유황 편석 등이 압연 방향을 따라 납작하게 퍼져나가 층상으로 된 박리층이 생기는 현상을 뜻함
강판의 두께 방향의 강도를 감소시킴
이 라미네이션이 있는 강재를 이용하여 용접을 하게되면 라멜라 티어 결함(고온 균열 중 하나)가 발생
4) 줄무늬 결함
연강 등을 인발하거나, 딥드로잉, 프레스, 압연 등 소성가공시 표면에 주름 등의 변형 모양이 생기는데 이를 stretchger strain이라고 함
상단 조질압연 링크 참조
7. 압연 공정에 대한 고찰
1) 압연 롤의 조건
기본적으로 내충격성과 내마모성을 동시에 가지고 있어야함
HR10 ~ HR80까지 구분된다
① 고온 내마모성, 내열성, 내산화성이 우수 (열간압연 목적)
② 인성 및 내열 충격강도가 우수
③ 가공면의 표면조도가 우수
④ HIP 처리로 내부 기공이 전혀 없어 고품질을 보장
⑤ 가동률 향상으로 경제성이 우수해야함
2) 제어 압연 냉각 (thermo-mechanical control process)
Nb, V, Ti 등 탄화물 생성 원소들을 미량 첨가한 저탄소 비조질 고장력강에서 열간압연과 냉각과정을 정밀하게 제어하면 압연상태에서 높은 강도와 인성을 얻을 수 있음
- 압연 전 slab의 가열온도를 가능한 낮춰 오스테나이트 결정립을 미세화시킴 (높일수록 조대화됨)
- 오스테나이트 영역 중 저온영역에서 충분히 압연가공을 통해 재결정 오스테나이트 결정립의 미세화를 함 (가공에 의한 미립화)
- 연신된 결정립계 및 결정립 내의 변형대 경계는 페라이트 핵생성장소로 제공되어 극히 미세한 페라이트 결정립이 확보됨
- Ar3 변태점 이하의 2상영역까지 가공을 계쏙하면 미변태 오스테나이트 결정립은 보다 연신되고 도입된 변형대 또한 밀도가 증가함.
- 변태가 완료된 페라이트 결정립 내에는 가공에 의해 전위밀도가 높은 아결정립이 형성되어 미립화가 더욱 진행됨
- 제어압연 종료 후 적당한 속도로 수냉(가속냉각)하거나 급랭하는 중 공랭(순환식)하는 등, 제어냉각을 통해 강도의 대폭 향상
- 페라이트 결정립 자체의 강화(전위밀도 증가), 미립화(가공에 의한 미립화), 펄라이트(베이나이트)분율 증가로 강화되는 것
가공열처리 (Thermo Mechanical Treatment), 오스포밍, 아이소포밍, 가공퀜칭, 제어압연
기본 열처리 담금질 (Quenching) 뜨임 (Tempering) 풀림, 소둔 (Annealing) 완전소둔 (Full Annealing) 구상화 소둔 (Sphericidizing Annealing) 재결정 소둔 (Recrystallization Annealing) 응력제거 소둔 (Stress Relief Annealing) 균
romanticdeer.tistory.com
파텐팅 열처리 (Patenting treatment), 블루잉 처리 (Bluing treatment)
기본 열처리 담금질 (Quenching) 뜨임 (Tempering) 풀림, 소둔 (Annealing) 완전소둔 (Full Annealing) 구상화 소둔 (Sphericidizing Annealing) 재결정 소둔 (Recrystallization Annealing) 응력제거 소둔 (Stress Relief Annealing) 균
romanticdeer.tistory.com
구상흑연주철의 페딩 현상, 페이딩 현상 (Fading)
금속 19-1-10 구상흑연주철 용탕에서 발생하는 패이딩(Fading)현상의 발생원인과 방지대책을 설명 하시오. 금속 16-1-11 구상화처리 후의 용탕유지에서 페딩(fading) 현상과 Compact Vermicular 흑연주철 (C-V
romanticdeer.tistory.com
열처리 결함, 퀜칭균열, 산화, 탈탄현상
12-1-9 열처리 결함의 종류 5가지를 들고, 그 발생원인 및 대책을 설명하시오 열처리 결함 1) 열처리의 정의 열처리는 소재를 가열, 냉각하면서 필요한 성질을 부여하는 작업 소재 상태, 가열, 온도
romanticdeer.tistory.com
'Mechanical Engineering Study > 소성가공' 카테고리의 다른 글
인발가공(drawing), 인발 가공 영향 요인, 인발력 (3) | 2024.10.28 |
---|---|
로터리 스웨이징(Rotary Swaging), 스웨이징(swaging) (0) | 2024.08.27 |
압연 - 열간압연강판 / 냉간압연강판 제조 공정 (0) | 2024.08.20 |
소성 이론, 응력변형률 선도, 재료의 성질, 슬립, 쌍정, 전위, 비강도 (0) | 2024.07.04 |
열간 프레스 성형, 핫 프레스 포밍 (Hot Press Forming), 핫스탬핑(hot stamping) (0) | 2024.06.13 |