Contents
- <기출>
- 1. 개요
- 1) 최적설계의 정의
- 2) 최적설계의 목적
- 2. 최적 설계의 방법
- 1) 설계 측면 (재료, 성능 등)
- (1) 치수 / 형상 / 위상 최적 설계
- (2) 재료의 최적 선정
- (3) 신뢰성 및 품질 확보
- (4) 유지 보수성 확보
- 2) 공정 측면 (가공방법 등)
- (1) 생산량에 따른 생산 형태 결정
- (2) 공정의 최적화
- (3) 스마트 팩토리, 유연 생산 시스템(FMS), 자재소요량계획(MRP) 최적화 등 시스템의 구축
- (4) 제조를 위한 설계 진행 (DFM; Design for Manufacturing)
- 3. 최적설계에 대한 고찰 (기출 23-3-3)
- 1) 최근 공작기계의 특성 (고속화, 고정밀화, 복합화)
- 2) 최근 공작기계의 특성에 따른 최적 설계 관점 문제점
- 3) 최근 공작기계 특성에 따른 최적설계 대책
<기출>
- 23-1-12 최적설계 제품을 생산하는데 고려하고, 확인해야 할 요소에 대하여 설명하시오.
- 23-3-3 최근의 공작기계는 고속화, 고정밀화, 복합화에 초점을 맞춰 개발되고 있는 추세이다. 이것을 실현하기 위한 최적설계 입장에서 대두되는 문제점은 무엇이며 이에 대한 대책은 무엇인지를 설명하시오.
1. 개요
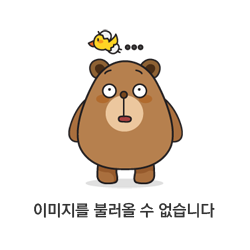
1) 최적설계의 정의
기계나 기계부품 등의 제작 설계를 할 때, 성능·재료·가공방법·코스트 등을 가장 알맞은 것으로 적용하는 것을 최적설계라고 한다.
원래 최적설계라는 개념은 손익분기점 같은 것을 계산할 때 해답을 빨리 얻기 위한 목적으로 경영분야에서 먼저 개발된 것이다. 기계분야에서 최적설계라고 할 때는, 기계나 기계 부품 등의 제원에 관하여 성능·재료·가공방법·코스트·납기 등의 설계조건이 규정되어 있는 경우, 그 범위 내에서 정해진 목적에 따라서 최적화를 도모하는 설계를 말한다.
설계 제원을 결정할 때는 주요한 패러미터를 설계변수로 하여 안전성, 유효성의 제약조건 내에서 기능·성능·코스트 등의 설계목적이 적절하게 실현되도록 설계변수를 최적화한다. 최적화수법에는 갖가지 방법이 제안되고 있는데, 최근에는 컴퓨터의 진보로 상세설계에서 수리계획법을 널리 사용한다.
[네이버 지식백과] 최적설계 [optimum design, 最適設計] (두산백과 두피디아, 두산백과)
2) 최적설계의 목적
최적설계의 가장 근본적인 목표는 비용 최소화를 통한 이익 극대화 / 고객 만족도 증대에 있다
① 성능 최적화
제품이나 시스템의 성능을 최대화
② 비용 최소화
동일 성능 기준 제작에 필요한 비용 최소화 / 수익 극대화
③ 제작 시간 단축
개발 시간 및 제작 시간 단축, 제작시 필요 비용 최소화
④ 품질 및 신뢰성 확보
시스템 안정성과 내구성 보장, 재고 감소에 도움
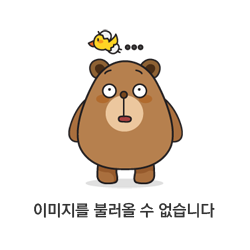
2. 최적 설계의 방법
1) 설계 측면 (재료, 성능 등)
제품의 목표 성능, 시장 요구사항, 제약조건 등을 고려 모든 것을 만족하면서 동시에 가장 합리적으로(저렴하게) 제작할수 있는지?
무게, 재료의 선정(염가의 재료, 수급 현황 고려), 부품의 가격, 메커니즘의 선정 등으로 최적 설계를 이룰 수 있음
결국 동일 성능을 더 저렴한 재료로(기계적 성질이 안좋은) 더 조금 쓰고, 간단하게 만들어서 구현해야 하기 때문에 설계적 리스크가 필연적으로 생기게 되며 이는 유한요소해석 / 실제 부품 내구 실험을 통한 검증이 선행되어야한다
(1) 치수 / 형상 / 위상 최적 설계
유한요소법을 이용, 동일 성능을 내는 최적의 치수, 형상, 위상을 결정
(동일 성능 기준 재료의 사용량이 적을수록 재료비가 절감될 수 있으므로)
(2) 재료의 최적 선정
동일 성능 기준 가장 저렴한 재료를 선정
제품의 신뢰성 기준 재료를 선정 (피로강도, 부식성, 마모성 등)
재료 원소재의 수급성을 고려하여 재료를 선정
(3) 신뢰성 및 품질 확보
단품 단위 신뢰성 테스트 (환경시험, 성능시험) 실시 및 신뢰성 확보가 필요
품질 확보로 비용 절감 필요
(4) 유지 보수성 확보
모든 제품은 보증기간과 수명이 있고, 해당 기간동안 비용은 지속 발생함
보증에 따른 비용 감소를 위해 assy단위 설계(모듈 단위 설계), 교체 및 유지 보수 용이성 확보(인건비 절감), 소모품 분리(재료비 절감)
2) 공정 측면 (가공방법 등)
제품 제작시 1) 제작 시간이 적게 들거나 (Cycle Time 최적화) 2) 제작 비용이 적게 들거나 3) 제작에 필요한 투자 비용이 적게 발생하게 하여 공정 측면에서 최적 설계를 이룰 수 있음
(1) 생산량에 따른 생산 형태 결정
- 기본적으로 금형 투자를 수반하는 프레스, 다이캐스팅 등이 생산성이 좋아 제품 당 가격은 저렴할지 몰라도 투자비가 대량으로 발생하기 때문에 제품 수량(생산량)에 따른 생산 형태를 결정해야함
- 제품 수량에 따라 3D 프린팅, 통가공 등의 비용 총합이 더 적을 수 있음
(2) 공정의 최적화
- 공정 순서, 설비 배열 등 인력, 장비, 공간의 최적 배열을 통해 총 생산 비용을 최적화 할 수 있음
(3) 스마트 팩토리, 유연 생산 시스템(FMS), 자재소요량계획(MRP) 최적화 등 시스템의 구축
스마트팩토리 (Smart Factory), 공장자동화 (FA; Factory Automation)와의 차이, CPS, ERP, MES
22-1-5 데이터 수집 측면에서 생산자동화(공장 자동화)와 스마트 팩토리(Smart Factory)의 차이점을 설명하시오. 22-1-8 스마트 팩토리의 생산시설 통합 소프트웨어 플랫폼인 CPS(Cyber Physics System)에 대하
romanticdeer.tistory.com
MRP(Material Requirement Planning, 자재소요량계획)
12-1-7 자재소요계획(MRP)의 장점과 단점을 설명하시오 1. 개요 1) MRP (Material Requirement Planning) 정의 제품의 생산수량 및 일정을 토대로 그 제품 생산에 필요한 원자재, 부분품, 공산품, 조립품 등의
romanticdeer.tistory.com
FMS (Flexible Manufacturing System, 유연생산시스템), GT (Group Technology, 그룹테크놀로지), 셀형 제조 방식 (
1. 개요 1) FMS (Flexible Manufacturing System) 정의 여러 가지 부품 유형들의 혼합과 수요 패턴 변화에 따라 조정되는 생산량에 유연하게 대응하기 위해 1) 여러 작업장에서 다양한 부품 유형을 동시에 처
romanticdeer.tistory.com
(4) 제조를 위한 설계 진행 (DFM; Design for Manufacturing)
부품 개수 최소화 (공용화 설계), 제품 셋팅 시간 최소화, 전용 조립 도구 사용 최소화 등
공정설계 (Process Design)
23-4-6 공정설계에 있어서 생산 적합성 판단과 관련하여 다음을 설명하시오. (a. 생산능력의 정의와 중요성 b. 생산관련 의사결정에서 고려사항 c. 생산능력 측정의 목적과 효과 d. 생산능력 측정지
romanticdeer.tistory.com
3. 최적설계에 대한 고찰 (기출 23-3-3)
1) 최근 공작기계의 특성 (고속화, 고정밀화, 복합화)
① 고속화
제품 생산에 필요한 시간을 줄이기 위해 점점 고속화되고 있음 (cycle time 감소에 따른 생산 비용 절감)
제품 생산에 필요한 각종 공정이 자동화되어, 총 생산에 필요한 시간이 줄어들고 있음
② 고정밀화
공작기계는 점점 고정밀화되어 제품의 공차 및 불량의 정도가 줄어들고 있음
③ 복합화
한 가지 장비로 여러 공정을 한꺼번에 수행할 수 있도록 공작기계는 복합화되고 있음
신규 장비 선정, 범용장비, 전용장비, 복합공정의 분류, 프로그레시브 금형(progressive), 트랜스퍼
17-3-4 제품가공 공정설계 수행 시 신규 장비를 선정해야 할 이유 3가지와 신규 장비를 선정할 경우 필요한 정보를 얻을 수 있는 방법 6가지를 설명하시오. 15-2-3 복합공정을 분류하고 장단점을 설
romanticdeer.tistory.com
2) 최근 공작기계의 특성에 따른 최적 설계 관점 문제점
- 열 문제
고속 가공 및 고정밀 가공시 열 발생이 증가하여 공작기계의 성능이 제약되거나 제품에 영향을 미침 - 진동과 소음
제품에 부정적인 영향을 미치고 공작기계 수명을 감소시키며 작업환경을 저해함 - 다른 제품으로의 유연한 전환 어려움
공작기계를 고정밀, 고속화하기 위해서는 특정 공정에 대하여 최적화하는 경우가 많으며, 이는 범용적인 기계보다는 전용 장비의 사용이 필요하고, 이는 공정의 전환이 어려움
3) 최근 공작기계 특성에 따른 최적설계 대책
- 재료 및 코팅 기술 개선
- 진동 및 소음 제어 기술 개선
- 범용 장비의 선정
'Mechanical Engineering Study > 공정설계' 카테고리의 다른 글
생산라인, 공장 레이아웃 (Lay out) 설계, 공자 기계 배치 방법, 공정별 배치, 제품별 배치, 셀룰러 배치 (0) | 2024.06.21 |
---|---|
시방서, 기술사양서, 요구사양도 (specification) (0) | 2024.06.11 |
공정설계 (Process Design) (0) | 2024.04.06 |
신규 장비 선정, 범용장비, 전용장비, 복합공정의 분류, 프로그레시브 금형(progressive), 트랜스퍼 금형(transfer), 복합 금형(composite die) (1) | 2024.04.05 |
생산계획 (Production Planning), 생산 능력, 생산 적합성 판단, 가동률, 생산 능력 측정, 생산 관리 (0) | 2024.04.04 |